Episode Description:
Building automation professionals, it’s time to master the final piece of the HVAC puzzle! In Episode 478 of the Smart Buildings Academy Podcast, we conclude our deep dive into HVAC systems with a detailed exploration of pumping and piping systems. Whether you're optimizing system performance, troubleshooting tricky setups, or designing advanced control sequences, this episode offers valuable insights to elevate your skills.
Key Topics Covered:
- The critical roles of flow, pressure, pumps, and valves in HVAC systems.
- Understanding decoupled loops and their impact on system performance.
- How to manage mixing valves to maintain temperature and flow efficiency.
- The hidden pitfalls of low delta T syndrome and how to avoid them.
- Practical strategies for sequencing pumps in primary and secondary loops.
Why It Matters:
Your ability to navigate the complexities of pumping and piping directly impacts system efficiency, troubleshooting accuracy, and client satisfaction. This episode provides the foundational concepts and advanced tips you need to take control of any hydronic system.
Click here to download or listen to this episode now.
Resources mentioned in this episode
- Free Technical Skill Assessments
- Smart Buildings Academy Workforce Development Program
- Smart Buildings Academy Courses
- Control Sequence Fundamentals HVAC Course
Podcast Video
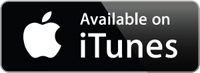
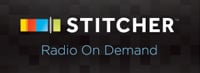
Transcript
Phil Zito 0:00
This is the smart buildings Academy podcast with Phil Zito. Episode 478 Hey folks, Phil Zito here and welcome to episode 478 of the smart buildings Academy podcast. In this episode, we're going to be talking about the final part of our HVAC series, and this is going to be about pumping and piping systems. So so far throughout the series, we have covered airside systems. We've covered hydronic systems, both on the chilled water and hot water side. We're going to be wrapping all this up with pumping and piping. As always, everything will be available at podcast smart buildings. Academy.com forward slash 478, once again, that's podcast that's smart buildings. Academy.com forward slash 478, and if you want to listen to the previous episodes in the series, you can go to podcasts that smart buildings, academy.com as always, we provide this content to you free every week, so if you can do us a favor, if this is valuable to you, please consider leaving us a five star review on Apple podcast or on Spotify really helps. If you're listening to this on LinkedIn, please go and share this and comment on your LinkedIn feed. Just click on the share button. And if you're watching us on YouTube, please consider hitting the subscribe button and liking and commenting on the video, because it definitely helps share the information. We would really appreciate that. With that being said, let's dive into the episode, pumping and piping. You know, up to this point, we've talked about hydronics, we've talked about hot water, we've talked about chilled water. We went pretty deep into how they work, but I've kind of skirted around the whole pumping and piping concepts, and that's for good reason, because I didn't want you to get bogged down with pressurization and decouplers and bypass valves and mixing valves and all that jazz too deeply. I wanted you to focus in on just the hydronic control concepts. Now we're actually going to look at the control of the pumping and the piping. So when we move into this, it seems that this can be a very complex topic. It's something that can lose a lot of folks, but ultimately, really it's just a couple concepts. It's flow, pressure and pumps and valves. I know I say that, and it seems so easy for me to say, but I will tell you that if you just focus in on those four things, and you really master and learn those four things, you'll be able to handle pretty much any goofy, crazy piping pumping scenario that's thrown at you. And, I mean, in reality, there's not that many that are going to get thrown at you. They're all normally derivatives of one of the big three, right? Constant Volume pumping, variable pumping with a mixing valve, or variable pumping with a decoupler. I mean, those are really kind of the three scenarios you'll run into when we're talking about pumping and piping. So as always, each concept in this podcast is going to build upon one another. So it's really important that you listen carefully. You know, rewind, pause, repeat. That's the beauty of the podcast. You can listen again and again but let's dive in. So the first thing I want to talk about, and I promise you, because this is not going to make sense at first, I promise you, we will circle back to this, and it will make even more sense as we get further into the episode. So if you get lost kind of in this first minute or two, just let this information kind of wash over you. Just absorb it, let it flow through you. My gosh, I sound like a freaking yoga master here. Let the energy flow through you. No but in all seriousness, just let it kind of flow through you, and it will make sense as we move towards the end of the episode. So this first concept is called tease law, and it simply states that whatever goes in the opening of a T must come out the remaining openings. So if you think about a T, right, we think about maybe a mixing valve scenario, where it can either continue back to the primary loop return, or it can go into the secondary loop. Well, whatever goes in that initial opening has to come back out. That's T is law. So what does this mean? Why? Why does this matter to us? Well, if we look at like a simple decoupler, which is basically just a pipe bridge where you have no valve, so you have a secondary loop, and then you have no valve, but you just have a straight bridge to the return. So essentially, it would look like two sets of T's and all included drawing in the podcast notes at building automation monthly com forward slash 190 so that you can kind of visualize this. But if you were to look at a decoupler, the flow would straight bypass the secondary loop, unless there was something pulling it through. Because what's going to happen is it's just going to go across the decoupler, because there's nothing pulling it into that secondary loop, the draw of that primary is going to go and pull it through. Now, one of the ways that we can deal with this right? One of the ways we can avoid this scenario is just simply putting a mixing valve in place, and so the mixing valve is going to go and forcibly divert flow into that secondary loop. So it's going to cause some constriction on that primary loop, some constriction is going to cause resistance, and now that flow is going to start to go through the secondary loop. We can increase that by going and adding pumps onto the secondary loop. Now the reason we add pumps onto the secondary loop is because of the resistance of the pressure drop induced by coils as we push water through coils, and the pressure drop induced by valves on the actual coils themselves that restrict the flow of water through the coil. So essentially, what's going to happen is on this tease law concept. As we start to have constriction, we're going to have the flow go into the secondary loop, and now we're going to have this flow go in there. But the problem is, is that that flow is going to be constricted, typically by cooling coils. Well, that's why we have this concept of pumping, and pumping is going to be sized to overcome pressure drops induced by cooling coils and other restrictions. Now, as you probably know, most secondary loops have pumps, so what happens if that secondary loop starts to close down. If those valves start to close down, well, now we start to be introduced to this concept of variable pumping. And variable pumping is where we vary the pump speed on the secondary loop. Because what happens is, as these valves are rather not. Close down, sorry, open up. As these valves open up, we are going to experience pressure drop. And that pressure drop is going to have basically meaning that we don't have enough pressure to push the water through all the coils, because now they're getting constricted. And so that pump is going to start to speed up and increase GPM, and that GPM draw is then going to start to pump more water through the coils. Now that's all well and good, right? We have a mixing valve, and the mixing valve, as we'll talk later, its main purpose is simply to control temperature, basically, either hot water or chilled water, to take that heated or chilled water from the primary loop and introduce it to the secondary loop so that it can then be pumped. So what I want to get really clear here, because I see a lot of folks mess this up. Mix this up is that the mixing valve purely exists to mix water to the secondary loop so that that water can condition the airstream of whatever coils it is being piped through. And it may not be coils, it may be radiators, or a bunch of things don't get cut off, caught up on that. Just realize that you're transferring a conditioned medium of water, or, yeah, water, we're just gonna talk about that, to a secondary loop, and that secondary loop is then going and controlling to pressure, and that pressure is being dictated by valves opening and shutting and the constriction of coils as water flows through it. All right, so we're clear on mixing valves and pumps and why we control both and the basically the process variables that would control both, and we'll talk more about this in the sequencing aspect of the podcast in just a second. But now that we understand this, I want to talk about kind of this decoupler scenario. Now I know I'm jumping to decouplers, which is kind of a complex topic, but it's okay, because once again, we're going to cover the basics of it, and then we're going to dive deeper when we talk about sequencing a little later.
Phil Zito 9:43
So decoupler, as I mentioned, is that straight bridge. But now, if we have a secondary pump on the secondary loop, what will happen is, as valves start to open up, the pressure is going to drop. That secondary pump is going. To turn up its speed to overcome the pressure drop, which is going to increase the GPM of that secondary pump more than the GPM on the primary pumps, which means you're actually going to start backdrawing water through and so decouplers can allow water to be drawn back into the secondary loop across the decoupler bridge. Once again, I'll give you an image that will make this make sense in the podcast. Link at building automation monthly.com. Forward slash 190 but when that happens, your sequencing should detect that the secondary pumps overpowering the primary pump, and you'll start to stage on more chillers and more pumps, more details on that a little bit later. But here's the big thing, the really big thing, and it is, why? Why a mixing valve? Why do we use this? Well, it's because of this simple equation right here, which is GPM one times temp, one plus GPM two times temp, two equals mixed temperature. So what that means is that as you start to times these things together, what's going to happen is that is going to create a mixed temperature calculation. And basically what this is, is that as we mix the primary and secondary water flows, we are going to essentially take 42 in the case of chilled water, 42 degree chilled water, and transfer it to a secondary loop to maintain a secondary loop temperature so that we can provide the accurate or the correct amount of cooling water to the secondary loop, but not over stress the primary loop. Now here's the deal. When we're doing this, it's really important that we have proper control of our pumping and proper control of our valve, because if we don't have proper control of either, then we can introduce a lot of issues. If we don't have proper control of our valve, we're not going to introduce enough chilled water. If we don't have proper control of our pumps, we're not going to get the chilled water that we're introducing through the coils so that they can actually condition the air. And this can cause all sorts of issues with our cooling valves that may make us think the air handler is not properly controlling but it's actually an issue with the loops themselves, and these sometimes can be very difficult to troubleshoot, especially if you have one or two air handlers that are really big, and they draw a ton of GPM and a ton of water through their coils, and you have a bunch of small air handlers, it may look like a set of air handlers is poorly performing because they're at the end of the line, When in actuality it's that these main air handlers are over you are basically taking all of the GPM, and then these air handlers that are down the line are thus starving, not getting enough chilled water. And you're thinking, there's an issue with air handlers, but it's actually an issue with the pumping and the piping, so we've got to be cognizant of this. All right, so continuing on, in order to handle this, first thing we want to do is control our mixing valve. And our mixing valve controls to a secondary loop temperature. Typically, that secondary loop temperature is either reset based off outdoor air in the case of heating, or reset based off of average valve position or average discharge error based in cooling scenarios. So that is our typical way of controlling a mixing valve. And then once we have that mixing valve under control, now we have to deal with another issue, because if our mixing valve, let's say it closes down right and it starts to close down, our GPM is naturally going to drop. So how do we deal with that? Well, we overcome that by utilizing a variable speed drive. The variable speed drive is going to allow us to increase or decrease the flow rate based on pressure drop, essentially differential pressure. This is going to help us avoid starving coils. Now, why are we doing this? Because we want to avoid this one condition in particular, which is called low delta t syndrome. Basically, delta t is the difference between entering and leaving temperature. It's the delta between two temperatures. It's ultimately, it's the delta between two things. But in our case, we're normally thinking about. Of entering and leaving water temperature, or most likely, entering and leaving air temperature low delta t. So what happens is that our cooling valves, or heating and cooling systems in themselves, are designed for a specific delta t. This is true for cooling coils. This is true for cooling towers. This is true for boilers and chillers. Basically, the concept is that if you're not properly transferring BTUs, indicated by not achieving your design delta t, then you're being inefficient. Now you could argue that if you're not hitting delta t. That could be because you just simply don't have a need for going and using that much BTUs in the case of heating or transferring that many BTUs in the case of cooling, absorbing BTUs rather. But if you're properly controlling your valves, then you should be maintaining your delta t because you're actually constricting the flow, but still allowing a full exchange of BTUs. That's at least the idea, right? Is you take only the volume of water you need to actually go and either transfer or absorb the BTUs from into the airstream. All right. So when we go and we put all this together, our mixing valves and our variable speed pumps, we're going to be able to maintain our pressure drop,
Phil Zito 16:30
we're going to get adequate flow rate, we're going to maintain our delta t and so that, my friends, is the main purpose behind us having mixing valves and variable speed pumps. And here's the thing that can get kind of nasty, and it's something you may end up troubleshooting, and I want to spend a little bit of time talking about it, and then we're going to start to move through some sequencing, and that is the concept of delta t at full load conditions. Now let's say you have, you know, cooling coil and is designed with a 10 degree delta t, but due to the coil being partially plugged, you're only able to get eight degree delta this means that even though your chiller is running at full load, we're only using 80% of that chilled water that is getting there. Now, this perceived lack of load is going to cause secondary pumps to run harder. We're going to end up potentially staging on additional chillers. It's going to cause all sorts of problems. In my experience, this is often due to someone bumping the balancing valve, you know, especially if you have those strainer balancing check valve multi, you know, the three purpose valves I'm talking about, someone bumps one of those, or someone doesn't properly clean the coils and they're getting plugged this is especially true with hot water. Is especially true with condenser water. You'll start to see these kind of things. And when this happens, it's actually a maintenance issue, not a control issue, but you need to be cognizant of it, because I will say, a good 10% of service calls where I've had improperly controlling air side systems, especially coils, was due to improper maintenance of the coils. Them getting plugged either by someone not changing filters, and filters getting sucked into the coils, or actually something getting into the water itself and plugging the actual tubes of the coil, or something someone bumping one of the three purpose valves, multi purpose valves, whatever you want to call them. So just be cognizant of all that. Alright, so let's move through some sequencing. Right? Let's first talk about primary pumps. Now we talked about pumping piping, etc, but what is the purpose of primary pumps? Well, they exist to provide water flow through the cooling or heating system, and they provide water flow through the primary loop. There are really two ways of controlling them, and it's constant volume or variable volume. Now, I will say most of the time you're going to see constant volume pumps, and most of the time you're going to see pumps in one of two. Actually, all the time they're either going to be in one or two of these setups, and that's either going to be in parallel or in series. Now series, basically what happens is the pumps, the water flows through one pump, and then it flows through the next pump, and then it throws flows through the next pump. There's no real way to isolate them, because they're in series, or there's in parallel, and parallel is where the pump is can be isolated and bypassed, and then there's several other pumps, so they're coming off of essentially a trunk line. Now what's happening here, typically, is we will have a pump dedicated to a machine, either dedicated to a chiller or dedicated to a boiler. Sometimes, though, we may just. Of a bay of pumps, and these pumps will rotate. They're not dedicated to any specific piece of equipment. You'll see this often in plants where they want to have true lead lag and switch ability for maximizing run time on the pumps. And the pumps are all sized similarly, and they're independent of the chillers or boilers, and so you'll see that sometimes you'll also see circulation pumps. So let's move on to primary and secondary loop control. Now, with primary and secondary loops, as I mentioned, the primary benefit is that we're going to shield heating and cooling systems from lower high temperature water, so that way, we're not shocking the heating and cooling systems, and we can actually condition that primary loop faster and then bleed that primary loop out to the secondary loop. It also allows us to contain that water, either the cooling or heating water, within a smaller primary loop and then mix that into a secondary loop as necessary. Now, typically we will have primary secondary loop control by having the primary pumps be constant volume, then a mixing valve and a variable volume secondary loop. So you'll see this as I mentioned, where the primary pumps come on, tied to a machine or basically in parallel, and then rotating through a lead lag. The mixing valve then controls to the temperature, either on a reset based on outdoor air in the case of heating, or a reset typically based on valve position or discharge air temperature, average in the case of cooling or a static dis secondary loop temperature. And so you're going to drive to that for the mixing valve, and then the VFDs are going to drive off of pressure. And you can also have a Truman response sequence based on pressure, based on average valve position, but I don't really recommend that. I've seen it utilized, but I don't recommend it. And then finally, we have the decoupled control. So decouplers, uh, real simple, right? What happens is, you have a primary pump, and it's typically running a constant volume, and it's tied to a chiller. So decouplers are, as far as I know, only for chillers. I've never seen a decoupler on a hot water loop. I don't know why you would use one. I may be corrected some of you may have seen decouplers on hot water loops. If so, hey, send me an email. I'd love to know about it. That would be really cool to see. I've never seen it. I don't even know why you would necessarily use it and not use a mixing valve, but decouplers are nice for primary, secondary chilled water loops, because what will happen is that you will have a chiller with its pump, and you'll go and you'll turn that chiller on, and that chillers can have Its pump running. Let's say it's 100 G I'm just using round numbers here, 100 GPM, and the secondary loop is got a secondary loop pump that can go from 100 to 200 GPM. And as that secondary loop pump VSD kicks in, the pressure starts to drop, valves start to open up. What's going to happen is that pump is going to speed up, and let's say it's GPM goes 150 Well, now we go back to T's law and the decoupler, and it starts driving or drawing water in reverse, back through the decoupler to the secondary loop, overpowering the primary pump. And so we turn on another primary pump, and that's our staging for our chillers. We stage a pump in order to overcome the GPM on the secondary loop, and then as the valves close down on the secondary loop, the pump slows down. The primary pumps start overcoming the secondary loop, and now we start to stage them down. So that is how a decoupled loop works already, folks, I hope you enjoyed learning about pumping and piping systems. I hope you found this information valuable as always. Everything is available at podcast. Dot smart buildings academy.com, forward slash 478, that's where you can go to learn more about this episode. Learn more about our control sequence fundamentals, course of which this episode and series is based on you can also go and learn more about our free technical skill assessment. If you're trying to figure out your skill gaps, definitely go and check that out. As always. If you found this valuable, please consider leaving us a review on Apple podcasts or on Spotify. Sharing this on LinkedIn by clicking the Share button and or liking and subscribing on YouTube and hitting the comment and the like button on the video. That really helps. We really appreciate it. Thank you everybody. We'll see you next week. You're gonna be seeing some new faces over the next couple episodes, our instructor staff is going to start doing. Podcast episodes, I think you're gonna find that to be particularly valuable. Give you some different perspectives and some different backgrounds. So with that being said, Folks, I hope you really enjoyed the episode, and I hope you have an awesome week. Thanks ton. Take care. Bye.