In this episode, we discuss how to use the pareto principle to focus in on the core skills you need to succeed in building automation.
Click here to download or listen to this episode now.
Resources mentioned in this episode
Training Video
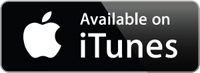
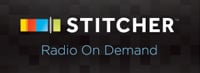
Transcript
Phil Zito 0:00
This is the smart buildings Academy podcast with Phil Zito episode 325. Hey folks, Phil Zito here and welcome to episode 325 of the smart buildings Academy podcast. In this episode, we're going to be applying the Pareto principle to controls and we're going to be talking about what do you really need to know. So in our previous episode, we kind of went through philosophy of being a controls tech, what behaviors tend to lead you to growth in your career. Now we're gonna switch gears, and we're gonna look more on the technical side of things and be like, Okay, what do you need to actually know, in order to succeed in building automation? Well, a lot of folks have a lot of different answers, you go into a group, that's mainly mechanics, they're gonna tell you, you need to be a mechanic for a couple years before you go into controls. You go into a bunch of programmers, they're gonna tell you, you need to know programming, you go designers, they're gonna say designing, you go with folks who have more of an IT background, guess what they're gonna say it. So initially, there's a bias on all sides, right? And we need to accept that. But if we look at where the industry is trending, that tends to be a decent road flare or signal flare, for us to kind of guide our careers, and figure out, okay, if we want to have a high paying job, we want to have a future that really is not dependent so much on someone being like, Oh, well, no, we have no need for that anymore. Then we want to pay attention to what the markets doing what the industry is doing. But at the same time, we also want to pay attention to what has stayed consistent within the market over the past several decades. So where do you start? Well, I like to start with what has stayed consistent. And then once I have figured out that I then look at where's the market going? Where's the industry going? So what stay consistent? Well, we still do point to point checkout, right? That hasn't changed. We still do functional test, we still create graphics, we still program building automation systems, we still do check out, we still do service, we still sell stuff, we still project manage things. Alright, so if we took all of those, and we broke those down into some core foundational knowledge sets, what would we have to know? Well, if you look at install, and I like to try to bunch these up, right, so if we look at installation, we'll look at Point to Point checkout functional test. And we look at service, we can bunch those up into kind of three buckets. And that would be electrical, H fac, and bas. And then if we look at design, and programming, right, that's more electrical, or sorry, HVAC, Bas electrical with a little bit of it mixed in there. And you can argue that some of the install and functional test and point to point checkout is it as well. Okay, so you got these things, right? We've got all of these different buckets, how do we start to pick out what we want from each bucket to focus in on from a skills perspective, let's look at the installer, service tack, and point to point check out functional test. So as we start to look at what is applicable to us in these areas. First thing that comes to mind, is do we do h back first, do we do bas first do we do electrical first which one?
Well, in my opinion, you should understand bas first, then H fac, then electrical. Now that flies in the opinion of a lot of folks. And maybe it's because I don't come from an H Mac background, I'm willing to concede on that potentially. But if you don't understand your basic tools that you can apply to an HVAC system from a controls perspective, then you're not going to be able to do anything you can understand H fac all day long. But if you don't understand what a controller is, what a protocol is, what different inputs and outputs are, then it's not really going to matter that you understand in great detail how an H vac system works. Now some folks will argue that by default learning an H vac system like learning a mixed air single path or learning 100% outdoor We're learning a central plant. In order to learn those things, you're gonna have to understand bas inputs and outputs, you're gonna have to understand bas controls. I disagree with that premise, because I've run into a lot of mechanics who were way more versed on mechanical systems than I. But they didn't understand basic safety circuits. They didn't understand sensor types, they didn't understand signal types, they didn't understand basic protocols. And so oftentimes, I would go on service calls. And these mechanics who knew the system wasn't working, because they didn't understand Bas, and the devices and the electrical side and things, they couldn't fix it. So in my opinion, you should know, the fundamentals of bas first, what should we really narrow in on we should understand bas architectures. So we should understand, you know, when do you use a supervisory device? What do you use a server? When do you use an advanced application controller? When do you use a three tier IP architecture? When do you use a four tier architecture? IP or non IP? When do you make these decisions? Then naturally, we progress downward from the top, you know, Supervisory device server device down, and we progress to the field controller in the IO. And we should start to understand control modes. Oh, what's the difference between stage control mode, floating control mode? On Off control mode? PID mode? I mean, it amazes me, I'll go and I'll post something on PID. And you would think and, and maybe you appreciate this, maybe you don't, but as a content creator, which largely we're a content creator, as an organization, as content creator, you would expect after you've created a piece of content, you know, four times, we've got four PID Loop tuning videos. And you know, they're free on YouTube. And yet, every time I talk about PID, I get tons of people who are like, where's the content for PID? And even though we've created it four times, so that shows me and based on my own experience, that there's a ton of people who don't understand control modes. Alright, so you go from supervisory devices, down to controllers, understanding controller types and architectures to control modes to IO to inputs and outputs. So how do the different inputs and outputs work? You know, when would you use a milliamps sensor versus DC sensor? What's an externally versus internally sourced? Why would you potentially maybe not want to power all your outputs from your controller? Why would you maybe want to, these are all things that you need to understand, in my opinion, before you ever get to the H fac point. Because let's be real, the reality is for a lot of people in their initial career in building automation, they're going to go out on a job site, and they're going to install what controllers, they're not going to go and install the sensors that's typically being installed by the electrical sub, they're gonna install the controllers, they're going to connect the wires to the controller if the electrical subs not already doing that, and then they're going to do point to point calibration and functional test.
It's at this point, at that functional test point that the check comes into play. Not before, not after, so H fac comes in, right at that functional test. Because up to this point, you can install controllers, you can wire up trunks, you can go and create different architectures, you can implement different IO devices. But at the point when you need to perform functional test, which means you need to ensure that the sequence of operations is actually performing according to what is supposed to happen. That's where you have to have a track knowledge. But what he acknowledged you have to have and this is a hot area of debate, when you get into conversations with folks on you know, Facebook groups or on forum groups, or Reddit, wherever. And you'll see it divided into two camps, you'll see folks who believe you need to have a you know, journeyman mechanical level knowledge in order to understand controls, and then you'll find folks in the other camp like myself, who believe you need to have a systems theory knowledge set. So what's the difference? Well, you know, a really solid mechanic is going to have systems theory, or at least they should, otherwise their apprenticeship is just totally screwed them over. But they should have a solid understanding of systems theory systems theory being like, Okay, if I have an air handler, and it doesn't have the right discharge, air temp, how does that affect vav boxes downstream from the air handler, or if I've got a chilled water plant And a bunch of air handler valves open up on the cooling coil. How does that affect plant pressure, stuff like that, that systems thinking that's inner connections between systems. The other camp will believe that you need to go and know how to change motors, you need to know how to go and install coils, you need to know how to go and braise pipe, install wells, hot tap, stuff like that, you don't, in my experience, need to understand that to be a successful Bas, installer or service technician, you really just need to understand enough to diagnose that it is a H fac system problem, and then get the appropriate people to fix it. And I think that's one of the problems we see in the industry, as far as talent development and talent acquisition, is you have these camps that are so divided. And you got a lot of legacy people of the belief that you need to have significant mechanical experience. And that precludes folks who have the right amount of experience in everything else from actually getting into this field. So from the installation perspective, from the functional test, from the point, the point, all that stuff, Bas first, it's facts, systems theory next, and then electrical knowledge, understanding things like Ohms law, AC versus DC, how transformer loading works, excuse me. So, for example, you know, you have a activated load and an activated load, you turn on a actuator, and the watt drawl from that actuator is going to increase when it's actually actuated, sometimes by as much as 100 to 200%. That naturally increases the VA load, but yet a lot of people will size VA loads for their transformers based on an actuated devices on loaded devices. And then they wonder when the system's working, why the transformer is sagging, why the secondary sagging and not performing. So having that baseline electrical knowledge of okay, these are the key concepts of electrical circuits, how they work simple circuit parallel circuit series circuit.
This is how safeties work. This is basic electrical safety. So where I'm getting at here is you don't have to be a master of H fac, of electrical, or even have bas. In order to be successful. In installation, functional test point point check out, what do you need, then you need to do a task matrix. So anyone ever asked me how do I succeed in XYZ role? I say, what are the tasks you do most often, in the case of an installer, you're lining out subcontractors, you're going and validating that sensors were installed properly, you're going and ensuring that point point calibration is done. You're mapping those controllers into a supervisory device, maybe even mapping them into graphics. So What skills does that require that requires those electrical an apex skills so that you know sensor placement and you know, that sensors are properly installed requires that BAs knowledge so that you understand what sensors should be used, what they should be connected to and what controller type should be used. So as you start to do that task matrix, you can break down your skills. And you're able to determine that, you know, maybe I don't need to get an electrical license, maybe I don't need to do a five year mechanical apprenticeship, maybe I just need to have XYZ things moving along. So the natural progression from installation or service technician is towards designer slash programmer roles. So if we think about that, how do we make that shift and I find that the shift to designer is much more difficult than the shift to programmer. Programming, if you have a mind for it is simply being able to interpret a sequence of operations and figure out what logical operators which logic blocks apply to what sequence language like if you came on a sequence came upon a sequence and it said that, you know, the fan will be enabled and must prove status within 30 seconds. Otherwise the system will go into alarm. Then, and you'd say and that's also dependent on occupancy. Then right off the bat you should say okay, that fan command is an AND block with occupancy and fan command. And then you can interrupt that and block with a status block with a time delay with a knotted input So that that status stays true until that status is not true, or rather that on delay makes, and then that nodded. Input basically breaks. So it's kind of hard to explain verbally, it's more of a visual thing to explain. But that's kind of how you think through from a programmatic perspective. Like taking logic and turning it into program not terribly difficult if you have a mind for it, and you understand the blocks. But design on the other hand, and this is the natural progression of careers, right is technician, designer programmer, that's typically how things happen. Well, how do you make that progression to designer because designer in my opinion, is the most difficult role in building automation. Because you have to have a solid electrical understanding, you have to understand bas devices and all of their capabilities. And you have to be able to interpret sequences and turn those sequences into schematic drawings, both from an electrical perspective, a mechanical perspective and a controls perspective. Because we need to show the BAS network layout, we need to show how that works, how it should be wired up, we need to show our electrical details so that our electricians can properly install. And we need to show our mechanical one lines so that folks can understand where device placements are supposed to happen. And we also have to do sanity checks on sequence of operations to make sure that they can even operate. So how do you get to that point? What
do you really need to know? Once again, it comes down to a job task breakdown? So first off task going and building our network riser? What do we need to understand we need to understand protocols and protocol limitations, right? You need to understand Rs 45 is the protocol behind BACnet MSTP. And the limitations associated with that right 32 devices a segment 3300 feet, polarity sensitive, etc, etc. Once we understand that, once we understand the specifics, in regards to networks on the serial network side, then we go to the IP side, we have to understand things like how those IP work, how would we connect to maybe a Lutron lighting system or to Crestron AV system? What would we do from an IP perspective? What would we do if we had a ring architecture for a bunch of IP controllers? What about a bus architecture? What about a daisy chain architecture etc. Understanding those things then enables us right to make the appropriate architecture choices. So that's our network riser. That's just one piece of this middle set. Then, right from there, we go to either depends on how you organize your drawings, either a system drawling and system sequence of operations, System Drawing and being a one line or we go to a controller drawing bill of material and electrical details really just depends. But if you go to a system drawing, right, you have to first be able to interpret mechanical plans, you have to be able to digest those plans pull the information from those as well as from the specification, have to be able to do sanity checks on those have to be able to read equipment schedules and understand like, Oh, it's this model control or this model rooftop or this model chiller, probably going to have to do this kind of one line. And then you have to be able to draw out mechanical one lines, you have to be able to actually represent visually, the mechanical system you are trying to go and implement. So you gotta have that mechanical knowledge you have to understand how systems are designed how sequences work and how they're selected. Once again, you don't have to understand how to install a motor. You don't have to understand how to install coil. But you do need to understand like what is hot that cold deck unit? What is a centrifugal chiller what is a variable speed chiller, what is the difference between a decoupled loop and maybe a mixing primary secondary loop what's a primary secondary tertiary loop etc. So you have to have once again that H fac systems theory you have to have it really high level then right so you got that and you're like hey, I got all that and I got my sensors and stuff for my bas knowledge I put them on the appropriate spots on the one line. Now you have to communicate all of that to an electrical sub so that they can properly install it. So now you need to be able to go research multiple catalog sheets for multiple products represent the installation of those different products in your control system. Because remember, each controller for each manufacturer is going to I mean besides for like RTDs and digital inputs is going to go in, wire up sensors differently, some controllers are going to source voltage, some controllers are not going to source voltage. So you need to be cognizant of this, you need to think through how all of this works. Okay, so you've got controllers, and you've got these inputs and outputs, and you've got this electrical knowledge for the inputs and outputs. And you need to now translate this to an electrician, who can follow these and install them. You also need to size transformers understand how many devices can go on a transformer, and things like that. So you have to have an electrical knowledge you got to have it can have mechanical kind of electrical and bas. That's why I think the designer role is quite possibly one of the most difficult roles, then we have programmers. So programmer role, what do you do with it? How does it work? How do you go and execute a program or role? How do you have the appropriate knowledge for a programmer role? Well, once again,
we come back to sequences, we need to be able to understand what's going on with sequences. And we need to have a baseline understanding of Bas, controllers and output types so that we can go and create programs that work. So what do we do, we have to first understand logic, we have to understand things like Boolean logic, switches, flip flops, gates, etc. Muxes, D, Muxes, all that fun stuff. And then once you understand what those logic blocks do, you have to be able to take that logic block and apply it to controls sequencing to a sequence of operations. And that, quite possibly, is the most difficult part of programming. actually writing a program once you know, the logic blocks just comes down to design patterns, right? So what do you really need to know when you're programming, you need to know design patterns, you need to know how to look at a sequence chunk, right. So maybe you have some start stop logic are some lead lag logic, or maybe you have state based control logic that switches between heating or cooling states. So you take these logic states, and then you're going to naturally translate those logic states to different program chunks, like, Okay, I'm going to use this order block in this PID block and the switch block. And that's going to make up a chunk that will say, you know, if I have call for cooling, or I'm below, discharge, air temperature, setpoint. And I'll enable this PID block. And maybe you're using like free cooling versus mechanical cooling, and you'll switch between the switch that will drive the outside air damper, and, you know, during mechanical cooling, that switch is going to drive the outside air damper to 20% or minimum outside air. And during free cooling, that switch is actually going to be connected to another PID loop that's driving to D at discharge, air temp. And you're going to be going and taking the value from that. So there's all sorts of kind of nuances in the sequence chunks. So how do you apply this to your career, quite simply to a matrix, kind of what I just did, I talked through three matrixes. If you're paying attention, I talk through three matrixes with you, one for install, one for design, and one for programming. So do a job task matrix job task analysis, figure out what job tasks and then figure out associated skills aligned to the shop tasks. That's the first thing. If you're teaching this, maybe you're running an organization where you're trying to teach some newer folks how this all works, go and do a job test breakdown. Figure out exactly where your team needs to perform what tasks, figure out where they're performing them inefficiently, and then train accordingly. So for example, if your team is doing a great job on vav boxes, then it makes no sense to go train them on vav boxes, right? Go and find something maybe they're underperforming on chilled water plant setup. Maybe they're underperforming on hot water plant setup. So go train them on that focus in on the job tasks that are non performing. Talk through this many, many, many episodes ago about using job codes and task codes on your projects to track performance so that you can appropriate analyze cost underruns and cost overruns so that you can appropriately train and develop your team and so that you can staff your team appropriately. Definitely dig into that. Okay. All right. If you have any questions, as always, do not hesitate to hit us up. I hope you appreciate these more kind of behind the scenes kind of thought process. podcast episodes are just about ready to wrap up this kind of series on that topic. And going forward next week we're going to be announcing that we're going to be doing Essentially, workforce development topic, a technical topic and a sales topic each week. So we'll have a running rotation. And we'll announce what days those are on Friday. So thanks so much for being here. I'll see you on Wednesday at 2pm Pacific time. Thanks so much, and I hope you all have a great rest of your day. Take care