In this episode, we discuss whether or not apprenticeships are still useful and how long these apprenticeships should last.
Click here to download or listen to this episode now.
Resources mentioned in this episode
Training Video
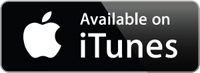
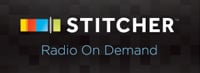
Transcript
Phil Zito 0:00
This is the smart buildings Academy podcast with Phil Zito episode 328. Hey everybody, Phil Zito here and welcome to episode 328 of the smart buildings Academy podcast. My sales director is at the Niagra Summit, which means no one is watching over me and what I talk about on the podcast. So I'm going to talk about a pretty controversial topic, which is do apprenticeships really need to last so long because this is something that people tend to get really heated on really quickly. If you even suggest that maybe 543 year apprenticeships are just way too long, and that maybe perhaps apprenticeships are happening so that you could have someone that you pay a little lower than you would pay someone else to do something that they could probably learned pretty quick. I know I've just probably upset a whole crap ton of people. And my team's not going to be happy with me for saying that. But the reality is, at the end of the day, I think that apprenticeships are valuable. I think OJT is valuable. But I think we are still operating on a model that was established decades ago that needs to change. And I don't think it's going to change because there's a financial motivation in drawing people out across many, many, many years. So what do I mean by all that? Well, if we look at building and I'm not talking about mechanical, or electrical apprenticeships, all right, those are things that are completely different. I'm talking about building automation apprenticeships, alright, so I want to be crystal clear on that. Because I know a bunch of you are gonna reach out to me and be like, Phil, you know, you can't learn all this stuff about these different systems. Okay, what I'm talking about is building automation. So going to building automation and looking at these multi year programs. And there's not really a union program or a true apprenticeship for building automation, there is more so these three to four year community college and college programs, and then these kind of hybrid work programs that are in existence. And that largely is because, you know, we have no licensure as a building automation professional to work towards. So since we have no licensure, and what we're doing in building automation can be very specifically narrowed down, should a apprenticeship really have to be that long? Well, I think reasonably, you should be able to train a building automation professional in three to six months to do a majority of what they have to do out in the field. I know a lot of folks are going to disagree with that. We're proving them wrong in our workforce development program. But that's not what I'm here to talk about. I'm not here to brag on our workforce development program. The reality is when I look at people who say, you know, and I did this, I went on LinkedIn the other day, this was actually months ago, and I posted about building automation and how we don't need to take three to five years for someone to be a technician. And then you have the regular old guard of you know, folks who've been in the field 3040 years posting, like, I don't know why they do this, but they post a laundry list of all these things you have to learn as building automation. And then as I look at that laundry list of things, I'm like, Okay, if we apply the Pareto principle to these concepts, and we ask ourselves, what do we actually have to know? Then we start to actually cut that list down by like almost a 10th. Because at the end of the day, majority this systems, we work with our vav boxes, right? We have vav boxes, a handful of air handlers, and maybe a chilled water plant and maybe a hot water plant. Now granted, can you point to decoupled loops, can you point to heat recovery, heat pump chillers and boilers? Can you point to primary secondary tertiary loops?
Phil Zito 4:21
Can you point to complex you know dual duct recovery unit? Yes, you can point to all of that stuff. But how often does all of that appear on a job? And therein lies the rub. I feel like we are making the industry inaccessible to talent, who would otherwise do quite well because we're placing these expectations upon them. And these talented folks are just going to leave and go elsewhere. If I have a computer background, if I can go and in nine months to a coding bootcamp and go work for a large software company, why in the world am I going to put in multiple years to work at a controls company for a quarter of the pay, it doesn't make a whole lot of sense. And that's why I think our approach to developing talent and apprenticeships in the building automation industry, the industry that I can speak to, because I've been in it, I can't speak to the mechanical industry, I'm not going to try not gonna try to speak to electrical apprenticeships, or test unbalance, I'm going to speak to specifically building automation, we should be able to take someone within three months make them able to perform point point check out mapping and controllers going and setting up supervisory devices, that should be doable. And then within six to 12 months, they should be able to write baseline programs, and almost run projects on their own. Because if we really think about what a project takes, we break it down into the simplest parts, right? We should, if we're running our business correctly, we should have a library of control stencils. For our design submittals, we should have a library of programming, we should have processes in place for installation, and calibration of our sensors and of our output devices. All of this should be in place to the point where pretty much everything we do should be rinse and repeat. So then part of running an effective building automation business, is having the processes established in order for your team to execute, right. So that's step one, a lot of companies don't have that nor if they do, do they enforce that. And there's where these multi year apprenticeships or development programs come about. Because since you have no processes for people to follow, people then are flailing about and basically reinventing everything on a job site. So you need this essentially super tech. Versus if you have a process driven organization, you can train people up on key skills, okay, understanding relay logic, understanding basic electrical safety, basic electrical transformer sizing, inputs and outputs, understanding basic input types, there's only so many basic output types, there's only so many controller mounting series, network controller setup. So that would be things like BACnet MSTP, Lon ft 10, Supervisory device discovery, mapping devices, adding them, all of those things put together. That is not four years of training, that is not four years of learning. And for those of you who think that is I think you're sorely mistaken. And I think you're unnecessarily holding back the development of others, as well as holding back the development of your business. If and organizations do come and talk to us about how they should implement a development program. And what I often tell them is to do a job task analysis, which when's the last time one of your companies has done a natural job task analysis? Probably not ever. So do a job task analysis, figure out what actually needs to be done, trained to those tasks, trained to those specific tasks. And you'd be surprised with some dedicated focus training, which is a mix between you know, instructor led training and OJT. You can get those tasks real, I don't want to say mastered but you can get competency real quickly. And that's a whole nother thing. Do not pursue mastery, pursue competency. Because there's a point of diminishing returns if you've ever heard me talk about like panel creation. You see if you go on Facebook, you go on LinkedIn, you see all these people making these beautiful panels and basically bragging and then I usually get flamed when I step in there, and I'm saying that's a huge waste of time. And people are like, well, the customer is buying this. I'm like, Well, yes, but I'm pretty sure the customer would probably rather you invest your hours into programming, your hours into graphics, your hours into their training your hours into functional test and point to point check out.
Phil Zito 9:13
Those are things that are actually going to make the system work versus having this like ridiculously over done beautiful panel. That being said, you know, if you have processes to do the programming, and you have templates to do the programming and templates to do the graphics, you have processes for creating these things, not from scratch, but actually from pre existing templates, then you can afford to invest in those other tasks like panel creation, or like doing a deeper functional test on your projects. Problem is, as I mentioned, many people do not have those processes. So this podcast episode Radler, rather than do apprenticeships really need to last so long, should be titled something to the effect of Africa. companies had processes and procedures, could they have someone who knows a lot less, doing the exact same job as someone who knows a lot more. And I know people don't like to hear that. But that's the reality with 100,000 jobs open at any given time for our industry, and people leaving faster than they're entering the industry. That is something that we're going to have to get comfortable with being uncomfortable about, which is this concept of, do I need the Super tech anymore, the super techs great, I myself was one of them, it's an amazing thing to have on your team that can do a lot of really cool stuff. But they're expensive. And they're very difficult to find. Versus if you really want to grow your building automation organization, if you really want to grow your career, like if I'm talking to someone who's a year into their career right now. Like, if you and I are talking over a coffee, I'm going to tell you to look at the projects you're working on right now, look at the tasks, you're doing nine times out of 10 develop a process for those tasks, and develop sub processes for those tasks for the people who are assisting you, for example, VAV box installation, I keep coming back to this because it's so common, and you have to forgive me I got a cold.
Phil Zito 11:18
But what you would do, you would lay out subprocesses for your electrical subs, right so that they know exactly what to do. And you would have a process for yourself, that process may be something as simple as getting with the mechanical, to mount the controller on the VAV box before it even gets put up in the ceiling. Yeah, that will save you a ton of time, it'll save your electrical sub a ton of time, then maybe have a process for how do you do check out on these boxes, maybe you can even train your electrical sub to do it. So that way you can move on to other tasks. That's what I would do. And if I were able to develop that, if you were able to develop that you would be coming a force multiplier for your organization. By creating these processes, you wouldn't replace yourself, you would actually free yourself up to do more complex work, you would free your organization up to do more projects, because everyone is short staffed right now. And you would become more valuable to the organization. So when you're looking at those processes, do a job task analysis and figure that out. But at the end of the day, and I've talked about this in my hammer Dad, we're going to talk about this every Monday we're going to talk about workforce development, we're going to be talking about talent management, talent development, we're going to be talking about strategies. The end of the day, I challenge you to let go of this concept that a building automation training path has to be a three to five year path. You know, I was talking with the one of the VPS at a very large system integrator. If I told you they were you'd know exactly where they are, they're multistate 100 million dollar plus system integrator. And he said that if we could take a technician from a five year training path and train them in three to six months, that would save them hundreds of 1000s of dollars. That's crazy to think about, but it's true. And he also said to me, why do we have to spend five years to put someone potentially, through, you know, a master's level program in engineering or programming, we're talking about like computer programming, but it also takes five years to teach them how to install a VAV box and controllers and stuff like that. And I agree. So I'm going to lay out today a plan for you that you can implement inside your own organization. Or you can implement this yourself if you are self performing person to go and develop yourself in three to six months. So ideally, you would use our training programs, but I'm going to set that aside. And I'm going to talk as if our training programs don't exist. And you're doing this yourself. First thing I'm gonna do is go get the Honeywell gray manual in the Honeywell gray manual. And once again, I'm assuming our podcast don't exist or any of our blogs. So that's why I'm referring to this. But I get the Honeywell gray manual. And I would master what inputs and outputs are and control processes and control modes. If you learn inputs, outputs, control processes and control modes, you're going to be ahead of the curve. On most technicians who are even at the three year mark, there's technicians who are at the 10 year mark, who cannot tell you how a PID loop works or how to tune one. So understand that and that's pretty straightforward. Then from there, I would get some electrical knowledge. I would understand obviously Electrical Safety OSHA 10 stuff, right. But I would understand circuitry, I would understand like several simple circuits, parallel circuits series circuits. I'd understand transformer sizing like apparent power versus real power, those kind of things. I would understand you know false DC versus milliamp versus volts AC versus ohms versus continuity, all these electrical concepts. Once I understand those things, that's going to enable me to apply that knowledge to my inputs and outputs that I learned earlier. Additionally, I've learned some basic installation. So I would do a job shadow and just realize how do people install airflow sensors, airflow, pressure switches, water flow sensors, water pressures, water flow, switches, actuators, relays, temperature sensors, averaging and probes, well, sensors, etc. And status and switches, etc. So I would learn all of those inputs and how do they get properly installed? Where do I place them? Okay, so you've got a pretty solid knowledge set there. Now you got to build upon that was some H fac theory, not h fac knowledge but theory. So I'd go from there, once again to the h to the Honeywell gray manual, as well as the old train and Johnson Controls, HVAC books, there's two of them, they're floating around, they're really hard to find. But both of them give really good knowledge of H fac theory. I would learn that and I would specifically focus in on like understanding sexual psychometrics, heat transfer, building pressure, infiltration and exfiltration. I would understand how do mechanical systems sequence like the system tree is something that I think folks should really understand which the system tree is started the terminal unit in the space, right, you're controlling airflow, which allows you to control temperature, humidity, co2, as you move from the VAV box, you move up to the air handler, then from the air handler, you move to the hydronic plant, and each one of these systems is symbiotic to one another. understanding that and understanding how these systems sequence shouldn't take you very long, you should be able to have a understanding of that within a matter of weeks. Now that you've got that baseline, and that baseline knowledge should take you three to four weeks to build. If you're dedicating yourself if you're spending like three hours a night focused on that, or if you're doing it at work, you should partner that with some OJT exercises, where you out on the job site looking at stuff, then from there, you should go and actually learn processes as to how to implement these things, how to go and actually do installations. Usually looking at the task matrix job task breakdown.
Phil Zito 17:31
What are you doing on a job, you know, Monday through Friday? What is that 20% of stuff you're doing 80% of the time, do that job task breakdown. And then once you've done that job task breakdown and you understand what you're doing, then you just need to develop processes and repeat and drill those processes, drill them again and again and again, until they become back at hand. And then you move on to your next level set of processes. But within eight to 12 weeks doing this with a good mentor, you should have a solid baseline of electrical a track and bas knowledge, you should have the processes down and know where to go and your BAS software to implement those processes. And you should find yourself like a highly contributing individual. It's not rocket science, it's not terribly difficult. I don't know why we still do things the way we do in the industry why we still take years to do this? I mean, I've been pondering this in my head for so long, like, you know, think about it. What if an owner instead of going and relying on this, like knowledge transfer in this ridiculous long process for their maintenance staff to be able to learn? What if they had QR codes that you could like take your phone, right and scan the QR code. And it brought up a video of how to do like an actuator replacement, or how to change a setpoint. Like literally you could have a binder with a bunch of QR codes, you scan them. And then it brings up a video and a walk through process. Sure, that would take a little bit of time to set up. But if you had a process in place, where every time you did one of those, you just documented it, excuse me, and super easy to create QR codes that link to URLs. So you could store this video, as well as store this process on a local server in your building. But if every time you executed something like a valve replacement, or a damper replacement or a filter change, you just took your phone which now are high enough resolution, filmed it talked through and then just did bullet points on the key points like step one, turn off the unit. Step two, pull out the filter. Step three. Ensure that you are matching the filter to the flow direction. Step four. Put the filter in step five, right on the filter when you changed. Step six, update the filter change log. If you just did that that, and you recorded a video boom, you now have a filter, change video, you create a QR code. And anytime anyone needs to do a filter change, they just scan that QR code, and they just watch the video, you've reduced the knowledge set that that person needs to have, in order to do that, by creating a simple process. And you could do this across the board. Like back when I ran an ops team, we would drill VAV box installs, we would have like a competition, when we would bring folks in for safety training, we'd spend 2030 minutes seeing who could install a VAV box and get it operational, or vav controller on a VAV box, get it operational the fastest. And we had a leaderboard as to who was doing it the fastest. And that's something you could do, you can gamify things. But at the end of the day, I hope you're seeing it doesn't require a really extensive, long drawn out program. So I know it was a little provocative in the beginning of this episode. But I hope you're seeing and agreeing with me at this point, that what we need to know can be condensed, and can be effectively condensed. And we can go and we can put processes in place that augment for experience. So with that being said, this is kind of what we're going to be exploring over the next several weeks on Mondays. Wednesdays, like I said, are going to be technical topics. And on Friday, we're going to be talking about sales related topics. I appreciate you all being here. I hope you all are open minded to considering a different way to develop talent within the workforce a different way to approach this. If this is something you're interested in, definitely let us know we do have a workforce development program that does all of this. But I don't want you to feel obligated to using our program. This is something that you could, in theory, develop in house if you're willing to make the time and monetary commitments to develop these. So at the end of the day, this is one man's opinion. Having been self taught in this industry, having seen a ton of people managed a lot of operations done a lot of different things. And I believe that it is time for us to potentially do something different. Alright.
Phil Zito 22:21
Thanks so much, folks, for being here. And I look forward to talking to you in future episodes. Please go to podcast that smart builders academy.com For slash 328. There will be some notes. You know, there will be the transcript. And if you want to check out any of our programs, there will be links to that as well. I appreciate you all being here. And if you have any topics you'd like us to cover in the future, do not hesitate to leave that in the comments. Thanks so much everybody. And I hope you have a great rest of your day. Take care