Episode Description:
In episode 463 of the Smart Buildings Academy Podcast, you'll discover how to transform your facility's operations using actionable strategies designed to improve efficiency, extend equipment life, and reduce downtime. This episode focuses on practical steps that facility managers and operators can take today to optimize their building systems. Whether you’re looking to cut costs, streamline your processes, or simply stay ahead of potential issues, this episode offers guidance that’s easy to understand and implement.
Key topics you'll explore in this episode:
Key topics you'll explore in this episode:
- How to simplify and organize your facility's critical documentation
- The role of preventative practices in minimizing unexpected breakdowns
- Tools for managing maintenance and tracking performance
- Proactive monitoring techniques to detect and address issues before they escalate
- Training tips for building a versatile and knowledgeable team
If you're ready to take control of your facility’s operations and avoid costly disruptions, this episode is a must-listen!
Click here to download or listen to this episode now.
Resources mentioned in this episode
- Free Technical Skill Assessments
- Smart Buildings Academy Workforce Development Program
- Smart Buildings Academy Courses
- Building Automation Training Guides
Podcast Video
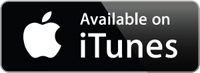
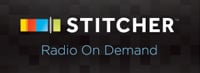
Transcript
Phil Zito 0:01
This is the smart buildings Academy podcast with Phil Zito. Episode 463, Hey folks, Phil Zito, here and welcome to episode 463. Of the smart buildings Academy podcast. In this episode, we're going to be going through the top five strategies to improve your facilities operations today using building automation systems. So in a previous episode, we went through how to optimize your energy. Today, we're going to look at facility operations as always. This podcast will be available at podcasts@smartbuildingsacademy.com forward slash 463, once again, that's podcast.smartbuildingsacademy.com forward slash 463, and I do want to let you know that today's episode is sponsored by our free technical skill assessment. So here at smart buildings Academy, we know that understanding your strengths and areas for improvement are critical in building automation, especially for building automation operators and building engineers. So our free skill assessment is designed to help you identify knowledge gaps and reduce the headaches you experience on a day to day basis. It's not a test, but it is definitely a valuable tool that will help you to enhance your expertise and awareness. So visit smart buildings academy.com forward slash skills, once again, that is smart building. Academy.com forward slash skills to take your free assessment today. All right, so let's go through these five strategies. So strategy number one, and it's one I see very often. And I want to let you know that pretty much all of these strategies, they are a journey. All right, it's not something that I expect you, or I think anyone expects you to be able to knock out in a single week, and it's something that is iterative, meaning you're going to continue to do it. So look at these. I guess a better phrase would be less strategies and more habits. So strategy slash Habit number one will be document your existing HVAC equipment and building controls. This is critically important in order for anyone on the outside, from a contractor perspective, to be able to help you, we need to know what's in your building if you want to get the most accurate quote for a retrofit, or you really want to ensure that you're optimizing. You know your systems, like you get an energy reduction goal, or you have some sort of reporting requirement, or you're trying to do lifecycle management of equipment, you need to know what you have. So going and documenting your HVAC equipment and building controls is critical. It's really not terribly difficult. What you do is you get your mechanical plans for your building. You annotate, hopefully you have a equipment schedule on there, and you'll go and annotate which piece of equipment has controls. And then if you do not have a controls drawing, you simply draw a one line of that piece of equipment. Sometimes you can just capture that right off the mechanical drawings. And you annotate where you have sensors, where you have actuators, where you have relays. And once you start to document that, then you put it into an electronic format, and that then becomes your baseline of your controls documentation. This is going to result in it being much easier for you to troubleshoot, because you'll know what you actually have. You'll know the inner relationships between systems. It's going to help you understand how your systems are configured, especially if you want to do some of the more advanced sequencing in guideline 36 or you want to do some sort of equipment staging or scheduling, and it's really going to help you to better plan for upgrades and replacements. So like I said, step one, you just want to gather your mechanical documents, if you have them. Step two is you're going to want to create a inventory of your HVAC equipment. Step three is you're going to want to create a one line of that piece of equipment and document where the controls components are. And step four is you're going to want to go and take this documentation and put it in an electronic format. This can look like everything from Microsoft Vizio AutoCAD to something as simple as making an image in paint and just saving it as a file, all right, strategy slash. Habit number two is implementing a preventative maintenance program. So we have a list of preventative maintenance activities that we utilize when we consult with owners and we help. Them build out what maintenance activities should they be doing? How often should they be doing them? And what does it actually entail? So what I encourage you to do is, once you have your systems, so you'll notice this is all iterative. Once you have your systems documented, then you want to create a list of your preventative maintenance tasks for those systems. And what that's going to look like at a high level is, you've got your systems documented. You're going to look at the HVAC systems and the control systems, and you're going to list out, you know, if this breaks, it has the most impact. So for example, if a filter switch goes down, yeah, it's going to impact your ability to know when your filters are dirty, which could damage the system long term. But it's not the same as a fan going down or a fan status going down. So there's a rank order to kind of prioritizing how you approach preventative maintenance. The benefits of this are, you know, early detection of potential issues. If you go and you do a preventative maintenance, which I'm going to call pm moving forward, not to be confused with project management, but if you perform a pm on a piece of equipment, so you go to perform a pm on an actuator, and you notice that, you know, one of the mounting brackets has come loose, and it's dangling by a screw or bolt that is early detention of a potential failure of that actuator, of that damper, and potentially of that unit, that obviously, If you detect potential issues, and you address them beforehand, then you have reduced downtime. You have reduced repair costs, because it's a lot easier to lubricate a fan, to replace a fan belt, versus to pull like bearings from a fan that destroyed itself, and then through bearings through a coil, which I've seen at a hospital. And naturally, if you do all of this, it goes and extends the lifetime of the equipment. So how do you go and address this? Well, assuming you have everything documented, the first thing you want to do is rank order, your systems, chillers, air handlers, those are going to be top priority, and then you have like, vertical, market specific systems, so the VAV boxes in an operating room, they're obviously going to take precedence over the VAV boxes in like the the entry lobby of a hospital. So rank order prioritize your systems, then rank order, prioritize the components of your systems. You can then go, once you have this in place, you can create schedules. There's all sorts of scheduling software for pm, so I'm not really going to get into it. You can use the building automation systems to monitor runtime, so you can see how long things run. You can use Filter switches, pressure switches, etc, to determine if maybe there's issues, if there's drift. You can even implement things like delta t across a coil to see maybe a coil is getting fouled up and, you know, plugged up and not properly going and cooling it'll or heating. It'll help you determine that. And then you got to keep records of maintenance, because it's all well and good to do maintenance, but if you don't have records of it actually being done, then, I mean, why are you even doing it? Because you don't know what you're doing. So okay, we've went we built out our controls diagrams, we've built out our documentation, we've implemented a pm preventative maintenance program. Now we want to implement a work order system. So this is more for your reactive maintenance, your troubleshooting calls. A work order system is simply going to go and allow you to have a way to categorize any requests that come in for maintenance. It's going to most likely have a link to the equipment schedule so the CMMS centralized maintenance management software. So you should have your equipment and all the nameplate data there. You should have your record of your PMS there, and your work order system should feed into that as well, and it will generate work orders based on reactive so trouble calls, hey, it's hot in here, it's cold in here, as well as scheduled PMS. This really is going to streamline your task management, help you forecast your labor out better.
Phil Zito 9:35
It's going to help drive accountability, because you'll know at any point in time what has been done what hasn't been done. It'll enable you to track maintenance activities. One of the most interesting stories I have was that a customer had a contractor who said they were doing maintenance, but when they actually went and looked at the work order tickets from the contractor, and then they compared that to the access logs on the card. Access. They saw that the contractor was badging in, and then one hour later was badging out, but was billing them for four hours. So by going and having your different systems integrated, you can actually get to a point where you can really start to have cost control. Now, how do you implement this? Obviously, this, well, maybe not obviously, I say obviously. Sometimes there's a filler word not to mean that it's necessarily obvious to you. I should probably find a better word, but hey, it's the one I use. So what you'll do is you'll go and submit some sort of request for proposal around a work order system. You'll get various vendors that will go and respond to this. Ideally, you'll want to figure out what's most important to you before the work order system. Does it have to work with your business systems? Are you a Microsoft shop? Are you a Google shop? Whatever? Once you figure that out, then you can write an appropriate RFP, and then once you have an RFP, the work order management folks can respond to that. Then you got to train your staff on the system you've got. This is hard to be honest, the step I'm going to talk about right now, which is taking all of your data and importing it into the work order system. But ideally, if you've been documenting things the way I've told you to in habit slash strategy. One you should be ahead of the curve. That's where most of the cost comes in. Training your folks on the staff is not too terribly difficult. As long as you've got the culture engaged and you've got buy in from your team, it shouldn't be hard to drive them to actually go and do the work. And then from there you want to integrate your building automation system and other systems for those automated work orders. Maybe something's offline, it goes and generates a automated work order, it being the work order system, all right. Habit number four, implement alarms, trends and reports. Okay, so up to this point, we've been documenting our control systems in our HVAC. We've implemented preventative maintenance. We have now started to consolidate our preventative and reactive maintenance with a work order management system. Now we want to try to get a little bit ahead of things, and so we're going to implement alarms trends and reports. Now, what is this going to do for you? Alarms are going if done right, because I've seen a lot of people do alarms wrong, but done right, alarms are going to give you indicators that systems are failing. Trends are going to show you that systems are degrading. There's a difference between failure and degradation, alarms are going to say, I'm out of set point. So you guys set point 72 but 76 in the space you've got an alarm doesn't tell you why. That's where the trend comes in place. And the trend is going to be watching data points over a period of time or a change of value, and will help you to determine why something's happening, and the reports allow you to run reports on all of these trends and alarms. This is really going to help you to get real time detection of your issues. It's done right? It can really help you stay ahead of things before the occupants even know the issues happening. It's going to give you historical data analysis, not only for identifying patterns, but also if you're trying to track any changes you've made and how that's impacting maybe energy efficiency or comfort. You can go and do that, and then automated reporting. You can set up reports. One of my favorite things to do, like with healthcare, is to run an automated report that reports on all patient rooms that are outside of the temperature parameters that were set by the CNO chief nursing officer. And once you know that, you can run that report every morning and you can come in and see, oh, these are the spaces we need to prioritize pming. How do you set this up? Well, you've got to decide on what parameters you want to monitor, typically, I say the things that impact the mission of your business. So most missions are focused on human comfort. Some of those human comfort conditions are tied to life safety, like in the case of healthcare, where human comfort is also tied to life safety, because having the appropriate temperature and humidity can reduce infections and surgery and in post op, can really help the healing environment by optimizing lighting, temperature, humidity, airflow, to help people heal. So determine what parameters you want to monitor, go and set the appropriate thresholds and alerts on those parameters and then regularly review them. So not terribly difficult to do it. It's more of getting to the parameters. So my kind of general rule is, what are the parameters that if this failed, it would dramatically impact your facility, and then work backwards from that to maybe like, Okay, if this failed, it wouldn't dramatically, but it would, and then you finally end up at, okay, if this failed, it's not it's a nuisance. So for example, if the ORS temperature or airflow or humidity is out of spec, you have to stop surgery. Or if the temperature is in an imaging room, I mean, that's your cash flow right there. If you can't run the imaging machine because of environmental conditions, then you're in a bad spot. So this would be critical parameters. But you know, the temperature of the lobby, while a pain in the butt and not the best look when someone walks in and it's hot in the lobby, is not going to impact the healing environment and life safety. So start to think through those. And then finally, habits slash strategy five is really to cross train. Is to take your electricians, your plumbers, mechanics and building operators, and cross train them. What does this even look like? Well, for electricians, you need to teach them Ohms law help them to understand low voltage systems so that they can help you know, your building operators maybe, oh, mount a sensor or help them trace out a calm bus that's got an issue or a break in it. Your plumbers, by teaching them how the control system should work, they'll understand the impact of maybe you've got a flow constriction, or maybe you've got someone literally bumped into a balancing valve, and that's why you're not getting proper flow in your secondary loop mechanics. Getting them cross trained with the building operators is really important, because it may not be a mechanical issue, it may be a controls issue, it may be an electrical issue, but understanding how to diagnose this, because this was kind of eye opening to me when I stepped into this field. The way you operate a purely mechanical system that's running off an electromechanical thermostat is very different than how you operate a mechanical system that's running off of a control system with maybe discharge, air, reset or trim and response or some sort of sequencing that you're not fully aware of so understanding this is critical. What you want to do is identify the key skills and knowledge areas that each one of these folks is going to be working in, create training plans and schedules. I usually like to go and maybe have an electrician shadow a mechanic or a plumber, or have a plumber, maybe shadow a mechanic, or have a building operator, maybe shadow a mechanic for a maintenance task, and that's a quick way to learn internally about these systems and what's done. The reason behind this, I do not expect your building operators to be mechanics or your electricians to be plumbers, but if they understand what everyone does, and they kind of get an idea for how things are supposed to work, then they can more quickly, faster, whatever is the proper way of saying it, determine if there's a potential issue and how to resolve it. Okay, so, like I said, everything will be available at podcast, smart buildings academy.com, forward slash 463, once again, that's podcast that smart billings academy.com, forward slash 463, I highly encourage you to implement these five strategies slash habits, starting with documenting your existing equipment and controls. Like I said, that's going to make things a lot easier for you, from inventory, from cost controls, etc. I encourage you to go into implementing a preventative maintenance program. This doesn't have to look perfect. It could literally be as simple as we're going to go check a system once a month. And you know, hey, that's better than, honestly, what a large portion of facility operators do, which is not even checking any of this. So then you go from there to implementing a work order system. You see all this is kind of building upon one another. Implement alarms, trends and reports, and then you cross train your electricians, plumbers, mechanics and building operators. In a future episode, we're going to look at the construction side of the business, and we're going to talk about, how do we establish standards? How do we take those standards into RFPs? How do we use those standards in our capital designs? How do we use those standards as part of our capital projects? And then,
Phil Zito 19:30
how do we put all of that together to create a campus slash building environment that is optimizing the capital, the money that it has both on the capital side of the business as well as the operational side. Thanks everyone for being here. Don't forget to check out that free skill assessment at smart buildings academy.com forward slash skills to determine where your skill gaps are, so that you can approach training and learning with data and not just with. Assumptions, thank you for being here and thank you for listening to the podcast. I hope you have an awesome week. Take care.