Episode Description:
In Episode 475 of the Smart Buildings Academy Podcast, we take a comprehensive look at the vital role of hot water systems in building automation. Whether you're troubleshooting a stubborn boiler, programming complex multi-system setups, or trying to master sequencing, this episode dives into the core concepts and strategies you need to succeed.
This isn't just another technical breakdown — it's a deep dive into real-world scenarios, practical tips, and common pitfalls, designed to enhance your understanding and control of these critical systems.
Key Topics Covered:
- The science behind hot water systems: What makes them efficient for energy transfer?
- Single vs. multi-boiler systems: How to approach sequencing and lead-lag control.
- Hot water setpoint strategies: Outdoor air resets, mixing valves, and system balance.
- Steam systems: Why they’re powerful, how to manage them safely, and their role in energy distribution.
- Avoiding common mistakes with flow, fuel, and control in hot water and steam systems.
If you're looking to refine your expertise in HVAC control sequences and elevate your building automation game, this episode is packed with insights and strategies tailored to your needs.
Click here to download or listen to this episode now.
Resources mentioned in this episode
- Free Technical Skill Assessments
- Smart Buildings Academy Workforce Development Program
- Smart Buildings Academy Courses
- Control Sequence Fundamentals HVAC Course
Podcast Video
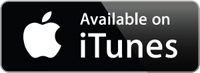
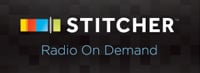
Transcript
Phil Zito 0:00
This is the smart buildings Academy podcast with Phil Zito. Episode 475, Hey folks. Phil Zito here and welcome to episode 475, of the smart buildings Academy podcast. In this episode, we're going to be doing things a little bit differently than we had planned, because at the time I'm recording this, it is mid December, we're actually going to flip things around, and we're going to be talking about hot water systems. So in this episode, we're going to talk about hot watering, hot water systems, how you sequence them, how you operate them. Everything will be available at podcast smart buildings, academy.com forward slash 475, once again, this podcast smart buildings, academy.com forward slash 475, as always, this episode is sponsored by our free online skill assessment if you are trying to close skill gaps in your team or in yourself, this is the perfect time to sign up for our free skill assessment at smart buildings academy.com forward slash skills. Once again, that is smart buildings academy.com forward slash skills. All right, let's dive into the episode. All right, so let's dive in to hot water. So we're going to start by going through hot water concepts, then we're going to go through a single boiler sequence, then we're going to go through
Phil Zito 1:19
multi boiler control, and then we're going to go through Steam. So we've got a lot to pack into this episode. So hot water concepts. What are hot water systems? Now, I know this may seem like a very obvious question. You may be like, Well, Phil, of course, I know what hot water systems are, but still, even as I researched this podcast episode, and as I taught this concept in our control sequence Fundamentals course, I still learned some things or got more so clarification on some things that were just not really misunderstandings, but just really seeing how these concepts kind of fit into the entire picture. So hot water is a mechanism. Water, in general, is a mechanism for transferring and absorbing energy. Because what we have to realize is that energy, mainly heat, is is BTUs, right? So we've got these British thermal units, and it's a measurement of energy. And what we're doing, essentially, when we are either removing heat from a space or transferring heat to a space is we are absorbing energy, whether it's the airstream absorbing energy from our hydronic system, or it's our hydronic system, in the case of cooling, absorbing energy from our Airstream. So hot water systems, all they are, are a mechanism of using some form of heat generation to then transfer that heat to the hot water system, and the hot water ultimately, and then that hot water is distributed throughout a building, either through radiators or coils or heat exchangers. There's a variety of different distribution methods, and we'll talk through all of those in this podcast. So heat, as I mentioned, is a form of energy, and this energy is measured by British Thermal Units. Throughout this podcast, you're going to hear me use these terms interchangeably, heat energy, BTUs, but essentially a BTU, a British thermal unit is the amount of heat required to raise the temperature of one pound of water by one degree Fahrenheit. So whenever you're wondering, man, what does this mean? When I see 1200 BTUs or 12,000 BTUs or 50,000 BTUs, what does that mean? Well, you just learned what that means. That means you have the capacity to raise the temperature of one pound of water by one degree Fahrenheit. So that kind of gives you an idea of heating capacity of your units. But why water? Why do we want to use water? Well, if you've ever worked on air side systems and tried to transfer heat via electric reheat it, you'll notice that it's very difficult. It takes a lot of energy to transfer heat to an Airstream. Now imagine if you were transferring heat to that Airstream and then sending that Airstream across a campus from a central utility plant to a building that's maybe half a mile away, and you're sending this heat over. And how much heat do you think would be lost by the Airstream? Probably a lot. And the beauty, though, of water and steam, which we'll ultimately talk about later in this episode, are that they can contain massively more energy in the form of BTUs, than air. Air has a is the. Least efficient transfer mechanism, and steam is the most efficient. The thing is, is that with steam, there's things like corrosion and special equipment that's required, and special control sequences, as we'll discover later, that make it more of a distribution rather than a actual control mechanism. We'll see it used for control later in this episode, but primarily it's used for distribution. What I mean by that is you'll have a central utility plant have steam, and it will distribute that energy from that central utility plant to individual buildings, whereas hot water is more of a control element, meaning that it'll go into coils, and you'll actually control the temperature in the airstream, utilizing hot water. So where do boilers come into play? And what are boilers? Well, as we'll discover in just a second, boilers are these mechanisms that transfer BTUs from a fuel source into the water or steam that is then delivered throughout the campus or building. So basically, you've utilized combustion, which is with fuel, gas, coal, wood, things like that. Or maybe you utilize resistance in the form of electrical heat and whatever you use. What happens is the hot water, or actually the returning less hot water because you don't want chilled water entering a boiler. There's a bunch of issues with that, but your you know lower temperature return water is then entering the boiler. It's heated up, and then it's supplied out to the buildings and or to the building itself. And the boiler is going to allow us to do this. So basically, how it works is a boiler has this thing called a burner, and that will combust gas or whatever, and will inject heat. And then there's these tubes that the water is flowing through. The Heat heats up the water inside the tubes, and then the tubes supply the water to the main pipe. The pipe then pumps out the water. The pump pumps out water out of the pipe into the building or into coils, and that's how we do heat with boilers. I mean, it's more complex than that, but we'll dive into that in just a second. But here's the deal, when we're working with boilers, we need to be cognizant. And I want you to remember this as we move into our hot water control, you need to be cognizant of several different constraints, right? You have minimum outlet temperatures. Maximum outlet temperatures. Need to maintain a temperature drop across the supply and return. We'll talk about why we need to do this later. You'll need to slowly warm up boilers. And this is going to affect secondary control. Morning, warm up multiple boiler setups, running things in unison, doing lead lag with peak control, all of those things. And then finally, hot water temperatures, they should be managed via piping, not or secondary. Hot water temperatures, rather, should be manager managed via piping, not via boiler control. That's something that a lot of people kind of misunderstand, and we'll talk about why, once again, later in the episode. And finally, lead lag is different than chillers, and we'll talk about chillers in next week's episode. But how you do lead lag on boilers is a little bit different. It's it's some cases similar, some cases different. All right, so let's go and talk about boilers. First. We're going to start off with a hot water boiler, a single hot water boiler. And where can we start? Well, typically, we're going to start by focusing on the three things we need to have control of. Now this is really important to understand, because when you're troubleshooting boilers, when you're programming boilers, if you don't have control of these three things, well, you're typically not going to have very precise control, and in some cases, you will not be able to get the system to run. And those three things are flow, fuel or power, and obviously control. So flow, flow is critical. Without flow, we can really mess stuff up. But the thing is, is, where does this flow come from? Early on in my career, I was starting a chiller in this was like the first controls job I did. I remember I was they were like, Go program the central plant in this high rise hotel. It was a hotel in intercontinental in I was in Chicago, I think, right by the airport, and I was supposed to go do these carrier chillers. And I was programming them, but I didn't know to open up the isolation valves. And because of that, the chiller just kept just making this God, awful noise and just dead heading. It was bad. It was it was really bad. Probably took a couple years off the life of that chiller, because I didn't understand the concept of flow. I really didn't understand how chillers worked. I was just looking at it. From a, oh, that's a binary enable. I'll just enable that, and then, oh, it's just a PID Loop. I understood PID loops and, you know, control loops, stuff like that. That can't be that hard, but I didn't have the systems knowledge that you're gaining in these episodes. So flow. I mean, in order for us to heat up the water, we've got to have water. And if we keep heating the same water, and we don't have flow, then we can actually hit our high limit on our boiler and cause problems, especially if that limit safety fails for some reason. So we primarily have to have our flow, which is we have to have our isolation valves open and we have to have our pumps turned on.
Phil Zito 10:37
Now, obviously we've got your pumps turned on, your isolation valves are open. You've got to have some way of heating the water. And this is where we have fuel. And it's really important to understand fuel, because I remember we had this old folks hospital in Dallas, and in Dallas we got this weird freeze that came through. It was very rare. I mean, we're like, sliding down hills. Some of you live in the north, like I do now, are like, man, that's pretty pathetic. But there are no plows. There are no salt. Everyone had their feet or feet had their heat turned all the way up, and because of this, what actually was happening is the overall gas pressure, which everyone was using for heat being sent to houses and buildings had dropped. And we didn't notice this, because we were getting enough gas pressure to enable the boiler and for it to go on low fire, but as soon as it kicked on high fire, it would trip off. And it was only after, you know, couple hours of troubleshooting that we thought, for whatever reason, to look at the incoming pressure. And this is why I say understanding flow fuel and control is so important, because you need to think through these processes and troubleshoot in that perspective. And so once we figured that out, we were able to work with the utility to get more flow to the actual building, so that they could stop taking the old folks out with ambulances from that old folks home. All right, so then we move into control. There's really three things we've got to control with, at least with a single hot water boiler. There's more things with multiple boilers, but typically we've just got to control our boiler, enable make sure the boiler is on, make sure our pump is on and make sure we've got a supply set point. Sometimes we will go and have a set point. Sometimes we will not have a set point. Boiler enables real simple. You just have a rib you and see you turn it on via a set of contacts. Boiler pump command pretty straightforward as well. The big thing is we tend to interlock flow status with the boiler enables so we will enable the pump and get flow status, and then enable the boiler. Sometimes the boiler has its own flow status as well, as well as its own circulating pump. And then finally, hot water set point. Sometimes we're able to do that. Sometimes we're not. Sometimes that'll be done by controlling the fire rate of the boiler. Sometimes that'll just be a two wire control set point, and sometimes that'll be like a BACnet or Modbus interface card. But there's multiple different ways of controlling that, and one of the things we need to be cognizant of when we're doing hot water set point control is that we typically want to run that hot water at a static kind of higher temperature, usually around 180 degrees. And then if we have a secondary loop, we will mix that hot water into the secondary loop, which then the secondary loop will be controlled either based off space temporary set or an outdoor air reset. And sometimes we'll have our primary loop temperature controlled off of an outdoor air reset as well. It just depends on how your building profile is, how the loads affect. It depends on how much heat loss you're going to have in the building envelope itself. There's a variety of variables that you need to take into account. But as I mentioned, there's really two ways we're going to do that, and that's either through supply temperature reset or mixing valve reset. So we're going to look at those two. I think we'll look at them in the sequence. If we don't, I'll come back to it. So our hot water sequence, single hot water boiler, right? Hot water system to be in operation whenever the outside air temp is below 60 degrees. So that's a simple comparative logic function that we're looking at. Oh, outdoor air via or versus, or compared to, man I can't speak, compared to this arbitrary, adjustable set point. Once that happens, the boiler is enabled and the pump, that is the primary pump, is scheduled to run. Notice, this is kind of inferring that there's a lead lag scenario, which is typical of boilers and chillers, where you have a primary pump that runs constant or run. As lead, and then you have a lag pump in case that primary pump fails and that lag pump comes on the lead and lag are both individually sized for the GPM requirements of the boiler or chiller and are rotated either on runtime or based on Start count. I prefer runtime. Some folks prefer start count, runtime, I feel gives you more accurate rotation. So once the pump is running, then it runs, and if it fails, the backup pump will start. The boilers will operate based on noticing that there's flow and an enable command, and there will be this hot water set point that will be reset based off of outside air. So as outside air increases, the hot water set point will decrease, and vice versa, as outdoor air decreases, the set point will increase. As I mentioned, this is typically 180 to 220 degrees that this reset takes place. So pretty straightforward right now we move into multiple boilers, and with multiple boilers, it's pretty much the exact same sequencing, except for some little differences, and those are primarily in how we enable the boilers, so you have Unison control, staged control and lead lag control. So Unison control is where both boilers, or all the boilers, if there's even more than two, are run in unison. Now the beauty of this is that this really helps you to not have to worry about bringing on a boiler, and potentially having to have that boiler run in low fire before it can be kind of added to the loop, because you don't want to be running, you know, really cold water through a boiler, or introducing cold water into a loop, or introducing really hot water into a boiler and sweating. There's all sorts of issues that you can have with a boiler, so Unison control largely avoids that. But this assumes, typically, that the boilers are the same size and that the water is the same flow rate. This does not work so well when boilers are of different sizes and different flow rates, unless the system's designed to handle that, and the reason why is that you start to lose some efficiencies. We'll see that we do something similar to Union control in lead lag peak scenarios, but that's more so of saying hey, we're way out of our design day conditions, we really need this extra heat, and in that case, the efficiency loss is acceptable. Staged control, this should be fairly familiar to any of you who have ever controlled DX coils. Any of you have controlled staged reheat. Basically, you're using a sequence or logic block that is driven off of a PID loop to go and sequence on boilers. And this is going to be, you know, last on, first off, kind of sequencing. And based on the amount of output from the PID loop, you will go and drive on boilers. And there will be a min off time and on time, and run time and all those things, right? Min, Max runtime, min max off time, and you'll gradually stage on boilers, and then you'll gradually stage off boilers, and finally, you have lead lag control, right? So this is very similar to lead lag control with the pumps, except for we're doing this with the boilers. Now,
Phil Zito 18:45
if we fail to meet set point in a purely lead lag scenario, nothing's going to happen. So I want to be very clear on that, and a lot of folks will get kind of thrown off by this. There is another version of lead lag, which is peak load conditioning. And basically what happens with peak load conditioning is we look at, am I not meeting set point, and if I'm not meeting set point, the lag device can either match the control conditions of the lead device. This is very similar for when we're using like centrifugal chillers. This is a very similar control, and it's also common with hot water boilers when we're doing lead lag with peak load conditioning, where it'll basically try to match the load requirements, or it'll maintain individual control. This is mainly meant to help in these really cold days. You see this kind of control up here where I live, where we can have these freak days where it gets negative 50 degrees Fahrenheit and yeah, in that case, you need all your boilers running completely all out in order to make sure that you are meeting your heating set points. So let's take a look at a sequence. So in this case. It's the hot water system is enabled for operation when the outside air temp is below six degrees. Looks pretty similar, right now, here's a little nuance. Each boiler has a circulating pump associated with it. This circulating pump circulates water inside the boiler, and then it's the primary pump that will then draw water from that circulating loop out to the primary loop. So right here, these boilers are going to be focused on maintaining a temperature, either a reset temperature as we talk through, or a constant temperature. Now, if the load exceeds the capacity of the lead boiler, then the lag boiler is pushed into operation as well. Once it's enabled and the circulation pump is running, it's then again to be operated to maintain the main boiler set point. So we see we're driving off of the same set point, but it's going to have its own individual control. So it'll control its own fire rate driving to the primary loop set point. Now once it drops below the capacity of a single boiler, the lag boiler is disabled. So it looks like we have some form of capacity calculation. Maybe we're looking at BTUs through BTU calculation, or maybe we're just they're calling it capacity, and we're simply looking at how far below set point are we whenever we're dealing with below and above set points, I like to use capacity control with BTUs. I feel that it's more accurate. It is harder to control, though, than simply having a set point. A temperature set point is always going to be easier because there's less calculations. So the hot water is then fed into a three way control valve, also known as a mixing valve. And this mixing valve is going to mix the hot water with the secondary loop. So this primary loop is sitting there in the central utility plant and is also being typically piped out to buildings, and within the building, there may be a plate heat exchanger, or there may be a mixing valve for a secondary loop. And what's happening is now you're taking that hot water that that hot temperature, and you're transferring it to the secondary loop that is then going to lower the temperature just a little bit, and is going to then feed that kind of 140 to 180 degree water out to coils. And the reason why is we want to use around 140 degrees versus 200 degrees, because, just like with steam, we will really overshoot our set point and over heat our spaces because of the temperature associated or how many BTUs are able to transfer into that Airstream rather and then the pumps are all going to be sized for full capacity on the primary side and on the secondary side, we will typically Have a discharge, or discharge a differential pressure sensor, typically at the end of the pipe run, and we will have VSDs or VFDs that are controlling to that differential pressure set point. That differential pressure obviously, is going to increase as valves close down, and is going to decrease as valves open up. Thus, as more valves open up, the differential pressure is going to decrease, and our pumps are going to increase their flow rate, their speed, in order to account for more water needing to flow through coils because of the resistance of the coils. So we need to be cognizant of that. Now, here's another thing that you'll see in some hydronic hot water loops that you don't really see in chilled water loops, and this is air dampers being interlocked with operations of boilers. Because boilers are utilizing combustion, whereas chillers are utilizing the refrigeration cycle and compressors and evaporators, etc, boilers are utilizing combustion. What do we need for combustion? In most cases, we need some form of air. Need some form of oxygen in order to combust the combustible material and create heat. And so thus, we need to make sure that we have outside air dampers that can open up, or dampers that are open to some air supply that the boiler can then draw air from in order to do its combustion process. Now we're moving on to steam. So steam is something that can be very scary. I mean, I've seen it cut through brooms. I've seen it burn people just by getting their hands even close to uninsulated piping. So it's scary stuff. You really got to be careful with it. But it's also friggin awesome for heat transfer, as let's talk about heat transfer and let's talk about states. Yes, when I talk about states, I'm talking about states of matter. So it takes 180 BTUs to take 32 degrees water to 212 degrees. So if you take freezing water and you heat it up to boiling, it takes 180 BTUs to do that right, one BTU per pound of water. But it takes 970 BTUs just to change one pound of 212 degree water into 212 degrees steam, that's four times the amount of energy just to perform a state change from water to steam at the same temperature. And this is why you see steam utilized on a lot of large campuses, because you can pump so much energy into the same mass of media, so or medium so you've got the steam medium and your pound, you're putting 970 BTUs into One pound, versus you putting, you know, 180 BTUs into one pound of water. So that's awesome, but it's also why it's so dangerous, because it transfers so much heat, and it's also why it's very hard to control. So steam is in two forms, right? You're going to have dry steam and we're going to have wet steam. Now, wet steam is what we want to avoid, as it's going to diminish the latent heat that we need for heat exchange. Because, remember, moisture makes it very difficult to transfer energy, and we want to transfer that energy so we want dry steam, and that's going to contain the most latent heat for us, so that we can utilize heat exchangers to transfer heat. We also are going to be focused on low pressure. We do not want high pressure. High pressure is things that are used for motorization, steam turbines, etc. We're looking at low pressure, which is we want our steam pressurized, but we only want it a low pressure because then we don't need crazy valves. We're not going to have to worry about crazy coils. And as I mentioned, we're not using steam to drive things. We're using steam to transfer energy. So heat transfer is either done through a heat exchanger, typically a tubular heat exchanger, not a plate heat exchanger, and or it's utilized directly via a coil in a Airstream. And this is more usually for preheat on large, 100% outdoor air units in very cold climates. And we'll use these things called one thirds, two thirds valves. And a one thirds, two thirds valve is pretty straightforward. It provides 1/3
Phil Zito 27:43
of the steam, and then the other is two thirds. Now, due to steam containing so many BTUs, you will get most of your heat transfer. Actually, when you open up that one thirds valve, because steam is pressurized, you're going to get a lot of heat transfer right away, and that's why we'll tend to control them. One thirds will open up based on the PID loop. Then it'll close down if it's not being met, and the two thirds will open all the way up. And then if it's still not being met, the one thirds will open up after the two thirds is fully open. That's how we typically do valve control with one thirds, two thirds coils. So typical heat exchanger is going to either have or a typical steam loop is either going to have a scaling strategy or a separate loop strategy. Scaling strategy is where you can have a single process loop and you're going to scale the one thirds, two thirds valves off that, as I just mentioned, or you can have a separate loop strategy, where you can have the one thirds valve that is driven off of a PID loop, and then you will have the two thirds that will open up afterwards. I don't like that separate loop strategy. It's just very difficult to control. I prefer that scaling strategy, as I just mentioned. Then one of the things we have to deal with with steam is condensate, because when we transfer the energy out of steam, it's going to change state back to water, and naturally, as I mentioned, we don't want wet steam, and water doesn't have the transfer capabilities as as well as steam does. And water can also plug the piping. So we will typically have a condensate pump at the bottom of the coil to pump out any condensate, and that condensate will typically be reclaimed and then utilized, either for heating water or for it can be utilized for domestic water heating. There's a variety of ways you can utilize condensate, or it may just be returned to the steam loop via a condensate piping. So there's a lot of things we can do with condensate. The most important thing is that we have a condensate pump, and we're removing it from the coil or the heat exchanger. So let's take a look at the steam sequence of operations, and then we'll close out this episode. All right, so steam, what's going on here is we have a tubular heat exchanger. Here, and what's going to happen is the heat exchanger is going to be enabled whenever an air handler is on. So basically, we know that the heat exchanger is being utilized for a building. Typically, it'll be sitting in a building, and then the steam will come into it, and you'll have a primary hot water or secondary hot water loop, whatever you want to call it, within the building, and that tubular heat exchanger will have one thirds two thirds valve. They'll open up based on a hot water supply temperature at that loop and or at the hot water loop. And then the one thirds valve and two thirds valves are going to open up based on how much heat that is required for that secondary hot water loop. So we're basically doing the exact same what we would do with coil, but we're doing that with a hot water loop and then the heat exchanger. I mean, it doesn't really do anything, it just kind of sits there, and we reset our hot water supply temperature based off outdoor air between 140 to 180 like typical, all right, folks, in this episode, we went through hot water systems. We went and tackled how they work, what they are, how they're controlled, and all the things you may need to know in order to effectively operate hot water systems. As always, everything's available at podcast smart buildings, academy.com forward slash 475 once again, that's podcast smart buildings. Academy.com forward slash 475 if you found this valuable, please do not hesitate to go and share this. If you're watching on YouTube, like comment and subscribe. If you're on podcast, Apple podcast or Spotify, please consider giving us a five star review. If you're on LinkedIn, please share this with your network and comment as well. Thank you so much. And being that I'm recording this for the week of Christmas, I hope you all have an awesome Christmas. You all take care, and I'll talk to you again next week. Take care. You.