Episode Description:
When disaster strikes, how do you assess the damage to your building’s critical equipment? Whether you're a building owner, facility manager, or insurance adjuster, knowing how to properly inspect damaged equipment can be the difference between a smooth recovery and costly downtime.
In Part 1 of this two-part series, we take you inside the equipment inspection process—a crucial step in evaluating damage from fires, floods, lightning, and physical impacts. You'll gain insight into what to look for, how to document damage effectively, and when to call in experts to ensure an accurate assessment.
In This Episode, You'll Discover:
- The different types of equipment that require inspection after an insurance loss.
- How to identify primary vs. secondary damage and why both matter.
- The step-by-step process for conducting a thorough equipment inspection.
- Common challenges you’ll face—like latent damage and time constraints—and how to handle them.
- Best practices to ensure accurate assessments and minimize costly mistakes.
This episode is packed with essential insights to help you protect your assets, streamline insurance claims, and make informed decisions when equipment damage occurs.
Click here to download or listen to this episode now.
Resources mentioned in this episode
- Free Technical Skill Assessments
- Smart Buildings Academy Workforce Development Program
- Smart Buildings Academy Courses
- Control Sequence Fundamentals HVAC Course
Podcast Video
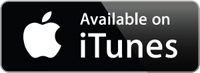
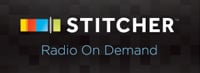
Transcript
0:00
Hey guys, Matt Scott here and welcome to Episode 480, of the smart buildings Academy Podcast. Today we're diving into the topic of equipment damage. 101, this is a two part series where, today we'll be breaking down equipment inspections involved with insurance claims and different types of equipment damage. The second part of this series will talk about a repair versus replace damage assessment for equipment. This series should be helpful for anyone involved in property claims, equipment management and also insurance adjusting. So whether you're a building owner, a Facility Manager or an insurance adjuster. This episode will provide you with a clear understanding of the processes, challenges and best practices for evaluating equipment after an insurance loss. So some key questions we'll go over in this podcast are, what is equipment? How do you identify damages? How do you conduct inspections? What information do you need, and when you should call an expert? So let's jump right in first. Let's define what we mean by equipment and equipment inspections simply put, an equipment inspection is a systematic process of examining machinery, devices or systems to assess their condition, functionality and any potential damages. So in the context of property claims, this means evaluating equipment after an incident like a fire, a flood or a lightning strike, to determine the extent of damage and whether repairs or replacements are needed. So here's an example. Let's take a look at this manufacturing plant. So you get a lightning strike, and at some point it shoots out a power surge, and so it could damage anything from your electrical systems to specific machinery downstream of that, such as motors, pumps, anything that might be attached to that equipment. So the role of an inspection in this case, would be to identify what's damaged, how severe and what steps are needed to be taken in order to restore or maybe even replace this equipment so that your operations are back to pre loss conditions, if that makes sense. So let's talk about the different types of equipment. So what constitutes as equipment? Well electrical equipment is primarily operated by using that electrical energy to perform their function, such as search, circuit breakers, transformers, switches, batteries, anything that uses that electrical energy to power something. Now, mechanical equipment is another type. Primarily you're using mechanical processes to power this machinery or equipment, such as engines, bearings, conveyors, compressors, anything that's moving. Now next we have electro mechanical so think about how it takes that electrical energy and it uses it in order to perform mechanical movement, such as electric motors, generators. You have your actuators, your pumps. And then there's really everything else. So you have in this picture, you have a MRI, so medical devices, dental chairs, you have maybe smart glass windows or decorative fountains with plumbing and filtration systems, anything that doesn't necessarily apply to these other three, we kind of fall, or it kind of falls under everything else. Now, since we've talked about different types of equipment, let's get into the different types of damage to that equipment that you might see on an insurance loss. Let's start with fire damage. Now fires can clearly cause a lot of damage. So we have primary and secondary damages are really the two type of damages when we see fire. So primary damages are are more visible, such as burn marks or melted components. That top picture here, you can kind of see a lot, lot of fire damage, right? Primary damage. Now, secondary damage is kind of hard to detect. In some cases, you'll see maybe some smoke residue that infiltrates the HVAC systems. You might have an odor and your carpet or. Or corrosion caused by smoke. It's important to identify both types of damage, because further down the road that secondary damage, maybe that res, that smoke residue and the HVAC systems and the ductwork, it might not seem like a big deal. You might not even notice it first, but it could snowball into something later on, so it's important to evaluate everything. Next type of damage we have is water damage. This can result from flooding leaks or even firefighting efforts. So sometimes you'll have the firefighters, you know, trying to put out that fire? Well, of course, they're using water, and so it's spraying down your equipment. And sometimes that equipment in the building is not rated for any kind of water, let alone gallons of water at a pressurized state. So when you're looking for water damage, look for signs of rust. In this picture, you can clearly see the circuit board has a lot of corrosion on it, or discoloration is another clear sign of primary damage. That primary damage is, in this case, a direct result of water so could be that short circuited electrical equipment direct corrosion, as I mentioned here. There's also secondary damage, which is important to be aware of because it's often delayed. So for instance, could be mold growth in the ductwork, similar to the fire. It could be structural rot or decay that might deteriorate over time. It's really important to understand the repercussions and to inspect and find anything or have any inkling of what might happen down the road. Then we have lightning damage. Now this is a tricky one, because the effects might not always be visible. The obvious is, as you can see in this picture, when lightning strikes, say, an electrical panel here and causes extreme burn marks. This is due to the extreme heat from the lightning. That's the primary damage, which can be seen pretty easily. However, lightning strikes can also cause latent damage, meaning the equipment may appear fine initially, but fail over time. This could be a power surge to your equipment. Maybe you don't power it on for a few days, and you turn on and the computer is not firing up the same way you might have an EMP or an electromagnetic pulse, or even material degradation to like insulation or wiring that you might not notice right away, all of that could be caused by lightning damage. Finally, we have physical damage. This is probably one of the easier ones to notice. This could be caused by impacts, like somehow this car flying into your building. You could also see a hail damage on your cooling coils, like this other picture down here to your air conditioning unit. As I mentioned, this is probably the easiest to detect. Now, common sides include dents, cracks or misaligned parts for building owners, equipment managers, adjusters or anyone conducting equipment evaluations. Documenting these damages is absolutely critical. Cannot express that enough photos, notes and even videos can serve as evidence of damage. Now that we've covered the types of damage, let's talk about the actual process of conducting an inspection.
8:52
Again, this is mainly focused on what happens directly after an insurance loss, but you can also think about it is if you need to inspect a piece of equipment that you suspect is damaged or it's not working properly, so we're just looking at it through the insurance lens. In this case. Now, a thorough inspection typically involves five key steps. The first is the pre inspection meeting. Before you even begin, you need to gather as much information as possible, like the type of equipment you're inspecting, what was the nature of the incident? So was it a fire loss? Was it a water damage? Is there corrosion on your piece of equipment? You also need to review maintenance records, photos, any documentation that's related to this claim. Now I want to talk about maintenance records for a second. They're paramount for any time you have an equipment loss, or Honestly, even if you're just not sure about a piece of equipment and. 20 years old, you need to know, and need to keep those kind of logs to understand if something needs to be done to it, or if this water, save water, gotten into your boiler, and we don't know if the boiler was damaged or not before the claim, it's going to be hard to understand the magnitude of damage based on that. Now, after you have your pre inspection meetings, you then can go into your visual inspection. Here you're you start by assessing the equipment, surroundings, so the environmental conditions, what exactly happened. Then you can start looking at your external and your internal pieces of equipment. Now you can then look at the equipment itself. Is there evidence of damage? Where was it in relation to the fire? For instance, are there visible signs of damage, like burn marks, rust, cracks, corrosion? And then once you see the outside of the equipment, then you need to start digging in to the mechanical and electronic components, so the circuit boards, the motors, pieces of equipment within that equipment that might have been affected by the fire hose or smoke infiltrating. Now, once the damage has been assessed, given that the anticipated functionality of the equipment, we go to step three, which is the functional testing. Now, if it's safe, test the equipment to see if it operates as it did prior to the incident. This can involve powering up a motor, running a system diagnostic or even testing individual components. Safety, of course, is key here. Never, I mean, never energize equipment if there's a risk of injury or even further damage to the equipment, so please make sure that everything is clear before it's energized. Now, as I mentioned a little bit earlier about keeping maintenance records when you're looking at equipment, I can't stress dye human tation. Now, when you're looking at equipment, I cannot express how important documenting everything is. So taking photos notes, I mean, that speaks 1000 words, right? This is not only helpful for your claim or if you're just trying to fix your equipment, but it is helpful also for your long term goals, because you're gonna have repair quotes, maybe replacement quotes, and also just further maintenance for that equipment down the road. I mean, if you saw smoke, might have gotten into a motor, and six months later that motor fails, you'll understand that was probably because smoke got in there. Now, once everything's documented from that inspection, we then get into our post inspection meeting. Now this is where you review your findings. Are there additional experts, like equipment consultants, that you need to bring in? So what's the next step? Does it need repaired? Does the equipment need replaced, or is there more evaluation by the OEM, as I mentioned, the equipment consultant? So we need to understand what those next steps are. Now, there's a few challenges in equipment inspections, right? One common challenge is the limited access to information. Now here we have the fire line do not cross so you it's not even been cleared, or the site hasn't been cleared, so can't even get in to look at that equipment. But even more so in terms of, as I mentioned, maintenance records or design documents. Having those available will help you understand the baseline condition of that equipment. So as a building owner, it's crucial to maintain those logs. Another challenge is latent damage, as I mentioned earlier, that could be with the electrical or mechanical systems. Not all damage is visible, and issues can arise weeks or months later. Then there's the issue of time constraints. So in the aftermath of an incident, there's often that pressure you get from stakeholders, maybe your other owners, to get those operations up and running as quickly as possible, which can lead to rushed inspections, obviously. And then finally, there's the challenge of specialized knowledge. Now, some equipment, like industrial machinery or medical devices, does require an expert. Piece to inspect that properly. So maybe if your maintenance guys don't have that expertise, we need to reach out to somebody. So knowing when to call a specialist can make all the difference. So what are some of the best practices for equipment inspections? First communicating with your investors, whether it's the equipment owner, a vendor or insurance adjuster, make sure everyone is aligned on the goals and scope of the inspection. Second, be thorough and methodical. Don't rush through the process. Oftentimes, you can use a checklist to ensure you're covering all those bases. If you need to call in experts, if it's the specialized equipment that you're not comfortable with looking at or assessing, don't hesitate to consult someone with the right knowledge and tools. And finally, as I mentioned earlier, please prioritize safety. This applies to both the equipment and the people conducting the inspection. Never energize equipment unless you're certain it's safe to do so. To wrap things up, equipment inspections are a critical part of managing claims and maintaining the systems for a building owner. So by understanding the types of damage, following a structured inspection process and applying those best practices that we mentioned, you can ensure accurate evaluations and better outcomes for all stakeholders. Thank you for listening to the smart buildings Academy podcast. We hope you learned a lot from this episode today. Be sure to check out the second part of this episode on whether you should repair or replace your equipment systems next week. If you found this episode valuable, please leave us a five star review on Apple podcasts or Spotify. If you're watching this on YouTube, please like, subscribe, comment, and if you're watching this on LinkedIn, please share this with your network. As always, this will be available on our website, at podcast, dot smart buildings academy.com, forward slash 480 Thank you, and we'll talk to you next week. Bye.