Episode Description:
When critical equipment in your building automation system is damaged, the decision to repair or replace isn't always straightforward. Making the right call can mean the difference between minimizing downtime and avoiding unnecessary costs—or dealing with ongoing failures and lost efficiency. In this episode, we break down the factors that drive this decision and provide a structured approach to evaluating your options.
In This Episode, You'll Learn:
- How to assess damage severity and remaining equipment lifespan.
- The financial impact of Replacement Cost Value (RCV) vs. Actual Cash Value (ACV)—and why it matters.
- Key cost analysis methods to determine the most cost-effective long-term strategy.
- How downtime, risk, and business continuity factor into the repair vs. replace decision.
- The role of energy efficiency, technological advancements, and compliance in modern equipment choices.
Whether you’re dealing with an insurance claim or planning for future resilience, this episode will give you the tools to approach equipment damage with confidence.
Click here to download or listen to this episode now.
Resources mentioned in this episode
- Free Technical Skill Assessments
- Smart Buildings Academy Workforce Development Program
- Smart Buildings Academy Courses
- Control Sequence Fundamentals HVAC Course
Podcast Video
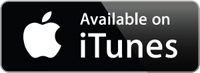
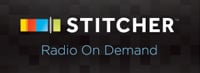
Transcript
0:00
Hey guys. Matt Scott here and welcome to Episode 481 of the smart buildings Academy podcast. As always, the information covered in today's podcast is available on our website at podcast dot smart buildings, academy.com forward slash 481 again, that's podcast dot smart buildings, academy.com, forward slash 481 also don't forget to hit that subscribe button and like this video if you haven't done so already, that way you'll get a notification the next time we release an engaging podcast. Video. This is part two of our series on equipment evaluation, which mainly pertains to insurance claims, and what building managers and owners should do when their equipment is damaged from a loss. Today, we're tackling a very important question, When should you repair equipment and when does it make sense to replace it? Now this isn't always a straightforward decision. It depends on factors like the extent of damage, financial considerations like replacement cost value or RCV versus actual cash value or ACV, and also a thorough cost analysis of both of those options. Some of today's objectives are to understand when to repair or replace equipment based on the extent of damage and other factors, as I just mentioned, we'll also evaluate financial considerations, including RCV versus ACV. We'll conduct a cost analysis for repair versus replacement decisions. And also it's important to identify key questions to guide your decision making process. Let's start with the big picture. Why is the repair versus replace decision so important? Now the goal of any equipment decision should be to maximize value of your asset or your piece of equipment, while minimizing costs and downtime to get that piece of equipment back up and running. This, of course, reduces your BI or your business interruption, which we'll talk a little bit more later in this podcast, but making a decision on what you do with your equipment after it's been damaged is obviously easier said than done. There's a few reasons this can be challenging. Now, when you're assessing your equipment, you need to have an understanding of the extent of damage. The condition of the equipment plays a huge role minor damage like a small electrical issue or cosmetic anything that doesn't affect the equipment's overall functional capacity can often be repaired at a fraction of the replacement costs, but we also get severe damage, such as a burned out motor or structural failure that may make a replacement cost a better choice. So let's take a look at the difference between these two AC units. Outside, one obviously has a little more damage than the other to the cooling coils. The first one we can see, it's pretty minor. There's some indentations, and we probably recommend a combing of the coils. Now, on the other hand, you can see the extreme damage from the hail here. Now I would recommend replacing the coil, and depending on the age of the equipment, maybe replacing the entire system just depends on, as we mentioned, multiple factors. One thing to note is the lifespan and performance of the equipment. Now, even if the repair is affordable, how much useful life is left in the equipment is a very important question. Now, we define useful life as the average lifespan of a piece of equipment. There's some different organizations out there that define this such as ASA or American Society of appraisers and Marshall and Swift. So even if a piece of equipment seems like it could be repaired at a decent cost, if it's at the near end of its life cycle, replacing it might be a better long term value. So another example would be, imagine you're assessing an HVAC system damaged in a flood. If the motor is corroded, but the casing and the other components are intact, a repair might suffice. However, if the system has been in operation for 15 years, or towards the end of its useful life,
4:45
a replacement might save you more money in the long run. Now let's talk about the financial side of the decision.
4:56
We have a replacement cost, value, RCV, a. Versus actual cash value. ACV, RCV represents the cost to replace the damaged equipment with a brand new item of similar kind and quality, or as often we reference it as lkq like kind quality and ACV, on the other hand, factors in depreciation, essentially the current value of the equipment based on its age and condition. So here's why this matters. If you're working with an insurance claim as kind of focused on here, the policy might only cover the ACV of the damaged equipment, which could leave you with significant out of pocket costs for replacement. On the flip side, if the equipment is critical to operations, and the downtime caused by repairs is causing you to lose too much money. We also refer to that as bi or business interruption, paying the difference to replace it might be worth the investment, and sometimes it's even in the policy under BI for example, let's say you have a commercial freezer that's eight years old and has sustained significant damage. The ACV of the freezer might be around 5000 while its RCV is 12,000 or its replacement, repairing it could cost, as we mentioned, around 5000 but if the freezer is nearing the end of its lifespan, replacing it for 12,000 might actually save you money and headaches, of course, down the Road. Insurance companies are pretty privy to this, and I would say, pretty lenient most times. Now, we'll go more into the cost analysis in a bit, but the key takeaway here is always know the RCV and ACV of the equipment before making a decision. It's a critical part of the equation. And speaking of equations, take a look at our ACV. It's really just a matter of our RCV, replacing that piece of equipment, and how much it would cost, minus the depreciation, or what we would use as in a percentage that gets us basically to our ACV. And then sometimes we actually have a FMV or a fair market value. This is when you take comparable pieces of equipment at that specific age and use it as a average cost for what it might be. Some policies will take the FMV or the fair market value, and some will give you the ACV. So make sure that you're aware of what your policy offers. Let's talk a little bit more about the depreciation methods that we use to calculate ACV. Now, the two most common ways to calculate depreciation are the straight line method and the useful life method. The straight line method is simply the piece of equipment's cost being spread out equally over its useful life or its expected age. As you can see in that graph, as the number of periods or the age of equipment ages the value of the asset equally decreases. The other more accurate way to calculate depreciation on a piece of equipment is the useful life method. It's typically more accurate because it uses historical data to predict the average useful life or an age life, age expectancy of the equipment. The useful life method takes the average useful life of the equipment, which is based on research from industry standards established by, as I mentioned earlier, Asa or American Society of appraisers or Marshall and Swift, and also the factors in the actual age of the equipment. As you can see in this chart. On the one side, we have the effective age in years, that's how old the equipment is. And then on the other axis, we have the typical life expectancy in years, that's the expected age or the useful life of the equipment. And this comes up with an age to life expectancy ratio on an expected percentage. So the result is a percentage of the depreciation. So when you're calculating ACV, you're taking this number, this depreciation, and subtracting it from what the actual cost of the equipment would be now or the RCV. Let's talk about some more financial considerations, mostly in terms of risk factors and how they can impact the business in ways beyond just financial costs. For instance. Is the downtime risk and business continuity, so how critical the equipment is to operations. If the equipment fails again after repairs, how much downtime will that cause? For example, a hospital HVAC system going down could have serious consequences, whereas a secondary warehouse unit might not be as urgent, we also have safety and liability considerations. So is there any risk to personnel, customers or operations? If that equipment fails, you could also have older or heavily repaired equipment that might not meet the latest safety standards. This could obviously pose a compliance risk. For example, you might have a failing electrical panel that could present a fire hazard if it was repeatedly repaired rather than just replacing it and being okay. We also, again want to take a look at your insurance policy and any warranty implications. So some repairs may void warranties or affect your insurance claims. If you got new equipment, it might come with better warranty coverage and lower insurance costs over time. And of course, in the business world, your reputation means everything that customer impact can make or break your business. So if your equipment is customer facing, frequent breakdowns, obviously would harm your business reputation. So for example, if you're running a hotel and you have an unreliable HVAC system, this could lead to negative guest reviews and over time, lost revenue. At the end of the day, risk should be weighed alongside costs. Repairing might be cheaper for now, but if it introduces greater operational risk, replacement could be the smarter long term decision. So let's get into the actual repair versus replace cost analysis portion. So we covered the basics, and hope you have a better understanding of what the equipment might be worth now. But how do you conduct a cost analysis for repair versus replacement? So here's kind of a layout how that would go. First, you need to estimate the repair costs. Now these repairs, obviously, are looking to repair that piece of equipment back to its pre loss conditions. So you need to get quotes from third party vendors, or in some cases, straight from the original manufacturer. Now this depends on the age of the equipment. Of course, because a lot of times, you'll run into a scenario where the equipment is obsolete, whether that's due to the company not making that equipment anymore, maybe it's outdated or outdated technology, or simply, maybe the company doesn't exist anymore. We run into that a lot. Of course, when you received an estimate for repairs, be sure to include not just the cost of parts, which we call material costs, but also the labor involved in repairing the equipment, and any additional expenses, like freight, maybe a crane rental if you need to put something up or use a crane to get to something, whether it's maybe a manufacturing press, and even need to think about taxes as well. Once you get one or two repair estimates for your equipment, you then want to make sure you reach out to the OEM, for the original equipment manufacturer for replacement cost of that piece of equipment, or, as we mentioned earlier, lkq, like kind of quality, pretty big term in the insurance world. Now this replacement quote or proposal includes not only the cost of that new equipment, but sometimes you'll have installation fees and any additional infrastructure upgrades that it might require. I mean, sometimes you'll have software, new software that's required, or maybe the equipment weighs more now, so you need to add additional structure support. Sometimes they're not considered upgrades, but necessary costs in order to keep up with today's standards and technology requirements. I mean, if you're replacing a computer from 20 years ago, obviously the hardware needs to be upgraded with it.
14:36
So once you have both the quotes for repair and replacing the equipment, some other things to consider are downtime, as we mentioned, bi and long term value of the equipment. Downtime can be a hidden but significant expense, especially in industries like manufacturing or healthcare, where equipment is critical to operations. So you need to ask your. Self. How long will it take to repair it? And will replacing the equipment minimize downtime? Sometimes you'll actually have a weed time of higher to replace it than you will to repair it. So sometimes, even though it might be cost effective to replace it, the BI that you get from repairing it at a faster rate is actually more significant, and then you would actually repair it, and maybe it's repaired in four weeks, as opposed to waiting, I don't know, 12, maybe even a year. In some cases. I mean, there are some pieces of equipment that are in very high demand, especially some transformers, HVAC equipment really just depends, so make sure that you're aware of the downtime costs, and then you need to evaluate long term value. Repairing may be cheaper up front, but if the equipment is near the end of its life cycle or likely to need frequent repairs, replacing it could save money over time. Here's an example to tie it all together. Let's say you're assessing a damaged air compressor. Repairing it would cost around 6000 or replacing it would cost 20,000 if the repair compressor is expected to last maybe another two years, but the new one comes with a 10 year warranty guarantee. Replacing it might provide better value when you consider the long term costs and benefits. So that is obviously, as mentioned, another factor when looking at the costs of replacing or repairing the equipment to help you make the right decision. Here are some of the key questions asked. What is the equipment's role and how critical is it to operations? Is it a critical component to your operations? So say you have a tornado hitting a FedEx building and half of your conveyor systems are down. Obviously, in that case, it's very critical, or can it be replaced with a workaround temporarily? So in that case, maybe we find some temporary conveyors in order to push that, push those products down, if it directly impacts your production or operation of the building. So say, maybe your HVAC systems are down or your boiler systems down, then addressing it quicker obviously plays a larger role in the repair versus replace conversation. Another key question, as we talked about, is that you really need to understand how severe the damage is. So going back to that AC unit outside, if hail damage hit the coil, and maybe 10% of the coil was bent or damaged, based on that hail, we would say that you could comb it or repair it, and it would be fine, but let's say that HVAC system got hit by a tornado, and it blew over and turned over, and all the components inside, everything that was welded, came off, and maybe your motor got flooded or got hit by hail, and that's the case. It's obviously a more severe condition, and we would consider replacing that. So understanding how severe is very, very important. Another question to ask is, what are the financial implications? Do you have the budget for replacement, or does repairing it align better with your financial constraints? Now, obviously your policy will help you with that as well. When you also need to ask, what's the equipment's age and life cycle? If it's nearing the end of its life cycle, replacing it may make more sense. But if it's almost brand new, obviously the depreciation on it is way less and it might be just worth repairing it. And in conjunction with that, we'll have to ask, Will this decision affect long term efficiency? So could replacing the equipment improve energy efficiency or reduce maintenance costs in the future? So if you're replacing it with a more efficient air handling unit that might save you more money from an energy perspective down the road. So that's another thing to look into before we wrap up. Let's take a step back for a minute and take a look at the bigger picture, which, of course, is how does the decision and whether to repair or replace the equipment impact the long term operation of a facility or business. In order to answer that, we have to take a look at a few different things. First, let's look at the operational reliability now frequent. Repairs might keep a piece of equipment running, but over time, the reliability of the equipment may decrease, which then leads to more unplanned downtime. I've talked about this before, having your maintenance team keep a log of service and repairs they've done before an incident happens can be pretty critical, and would help both the insurance company and your maintenance team understand the condition of the equipment ahead of time and also assist you in anticipating future repair costs that you might encounter if you go back to that piece of equipment. So of course, if you're thinking about a new piece of equipment, it is going to have a higher upfront cost, but in terms of reliability, of course, it's going to have a greater long term stability and, most likely, fewer disruptions over time. Now this isn't necessarily part of an insurance loss, but let's also think about the energy efficiency considerations pertaining to your equipment. So older equipment may not meet current energy efficiency standards, which could result in higher operating costs. Newer models often have advanced technology that's designed for reduced energy consumption and cost savings over over time. So for instance, let's think about your boilers in your building or your furnaces, they often operate around what 60 to 80% efficiency. And nowadays, your modern condensing boilers are around or exceed 90% efficiency, same with your air conditioning units, many of those pre 2010 AC units are still using our 22 refrigerant now, of course, that's been phased out due to our environmental concerns. Now these older models tend to have lower SEER ratings or seasonal energy efficiency ratio compared to the modern units, which what have around a seer of 16 or higher even we also need to look at technological advancements so newer equipment may integrate better with the smart systems and automation that we see in today's buildings such as smart thermostats and sensors, all of these are AI driven systems that are designed to optimize the HVAC performance based on occupancy and real time data. And then we have our older HVAC units that might benefit from retrofits like VFDs or variable frequency drives on your fans or your pumps, which might improve the efficiency without a full system overhaul. So you do have to weigh your options with the repair versus replace. You might have these new systems that integrate better, but also you might save money by getting those retrofits with the VFDs. So repairing outdated equipment might meet your short term needs, but replacing it could ensure long term compliance with the new standards and technology. And speaking of standards, we have our regulatory and compliance factors. Of course, safety always means everything. Industry regulations around safety, environmental impact and efficiency are always evolving. So what is your older system meeting the future industry standards? Maybe, maybe not, something to think about by considering all of these factors here, you're not just making a financial decision for today. You're making a strategic investment in the future of your operations. Now let's go to our summary of what we've learned today to wrap things up, deciding whether to repair or replace damage equipment is rarely black and white. It's about weighing the cost, the operational impact and the long term benefits.
24:38
We need to make sure that we evaluate damage extent and remaining lifespan before deciding we need to use the RCV and ACV to assess financial implications, we need to make sure that we're conducting thorough cost analysis for immediate and long term impacts. And as we saw in the last slide, we. Need to use those key questions to make informed, practical decisions. Thank you for tuning in to this episode on smart buildings Academy. If you have any questions or topics you'd like us to cover in future episodes, feel free to reach out to us. If you found this episode valuable, please leave us a five star review on Apple podcasts or Spotify if you're watching this on YouTube, of course, like comment and subscribe. If you're watching this on LinkedIn, please share this with your network. We want to reach out to as many people as we can. As always, this will be available on our website at podcast dot smart buildings, academy.com forward slash 481 one last time, that's podcast dot smart buildings, academy.com forward slash 481 until next time, I'm Matt Scott, reminding you to make smart, informed decisions for your equipment and your operations. Thank You.