Episode Description:
Estimates shape the success of every building automation project. Knowing how to assess labor, materials, and subcontractor needs can determine your profitability and project outcomes.
This episode gives you a practical look at the estimating process, revealing what matters most when preparing accurate and competitive BAS proposals. You’ll gain a sharper sense of what to look for, where the risk lies, and how to improve the quality of your estimates.
Topics covered in this episode:
-
The essentials of reviewing specifications and drawings
-
System-level thinking for identifying control scope
-
Device takeoffs and labor planning fundamentals
-
Coordinating with subcontractors and managing scope
-
The role of overhead, risk, and markup in the estimate
Listen in to sharpen your approach and strengthen your project planning.
Click here to download or listen to this episode now.Podcast Video
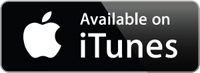
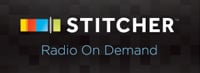
The Overlooked Skill That Can Make or Break Your BAS Projects: Controls Estimating
Project success in building automation often begins long before technicians arrive on-site. The controls estimate sets the direction, budget, and technical expectations for everything that follows. When done correctly, it ensures that projects are properly scoped, priced competitively, and executed with fewer surprises. When done poorly, it can lead to cost overruns, scheduling issues, and frustrated clients.
Controls estimating requires a mix of technical knowledge, attention to detail, and practical judgment. Understanding how systems operate is just as important as knowing how much a device costs. A complete estimate accounts for every element needed to deliver a system that meets the specification and performs reliably in the field.
Key Elements of Controls Estimating
A controls estimate begins with a thorough review of project documents. Specifications, mechanical and electrical drawings, and any client-provided requirements form the backbone of the estimate. These documents provide guidance on system scope, integration expectations, and labor responsibilities. Misinterpreting or overlooking these details can cause serious gaps in the estimate.
From there, estimators identify which systems require control. This could include air handlers, VAV boxes, boilers, chillers, lighting systems, energy meters, and more. Each system brings unique device and labor needs. For example, a constant volume air handler requires different programming and commissioning hours than a VAV system with advanced control sequences.
Building the Takeoff
Device selection is an essential step. Estimators must list each controller, sensor, actuator, and interface required for the job. They also determine whether the project calls for network equipment, user interfaces, control panels, or cabling. Each item has to be specified with accuracy to avoid budget issues or field changes later on.
Once the device list is established, labor estimates are developed. Labor covers everything from programming and panel fabrication to point-to-point checkout and commissioning. Project management, engineering review, submittals, and documentation support must also be factored into the hours. Estimators use historical data, rules of thumb, and local office preferences to generate realistic labor forecasts.
Coordinating with Subcontractors
Subcontractor pricing is a major component of the estimate. Most BAS contractors rely on electricians to install devices and run wiring. On retrofit or hydronic jobs, mechanical subcontractors may also be involved. Successful estimating requires clear communication of scope and responsibilities. Providing device schedules, mounting details, and project drawings helps subcontractors price the work accurately. Estimators should always confirm what is included and clarify who is responsible for hardware, wiring, and conduit.
Integration work may also require specialty subcontractors if the project includes legacy systems or complex protocol translation. While less common, integration needs can add cost and complexity that must be addressed early.
Finalizing the Estimate
The final estimate includes markups for overhead, contingency, and profit. Overhead covers costs like tools, vehicle use, and general operations. Contingency is reserved for risk areas in the scope or unclear specifications. Profit must be set at a level that supports business growth while remaining competitive.
Before submission, estimators must verify that no scope gaps exist between trades. This includes power wiring, device mounting, and network connectivity. Catching these early protects your margin and reputation.
Why This Skill Matters
Controls estimating is a discipline that rewards precision and experience. It supports business development, strengthens relationships with clients and contractors, and helps project teams deliver work that is both profitable and technically sound. Developing this skill helps professionals advance in their careers by connecting field knowledge with business strategy.
This is not a job reserved for salespeople or estimators alone. Technicians, engineers, and project managers who understand estimating are better equipped to scope jobs, communicate expectations, and spot issues before they become costly mistakes.
As building automation projects grow more complex, the ability to produce clear, accurate estimates is more valuable than ever. It is a skill worth investing in, and one that directly impacts your success on every project.
For a deeper discussion and insights from the field, listen to Episode 490 of the Smart Buildings Academy podcast